Backlash 101: How to Recognize and Rectify in CNC Operations
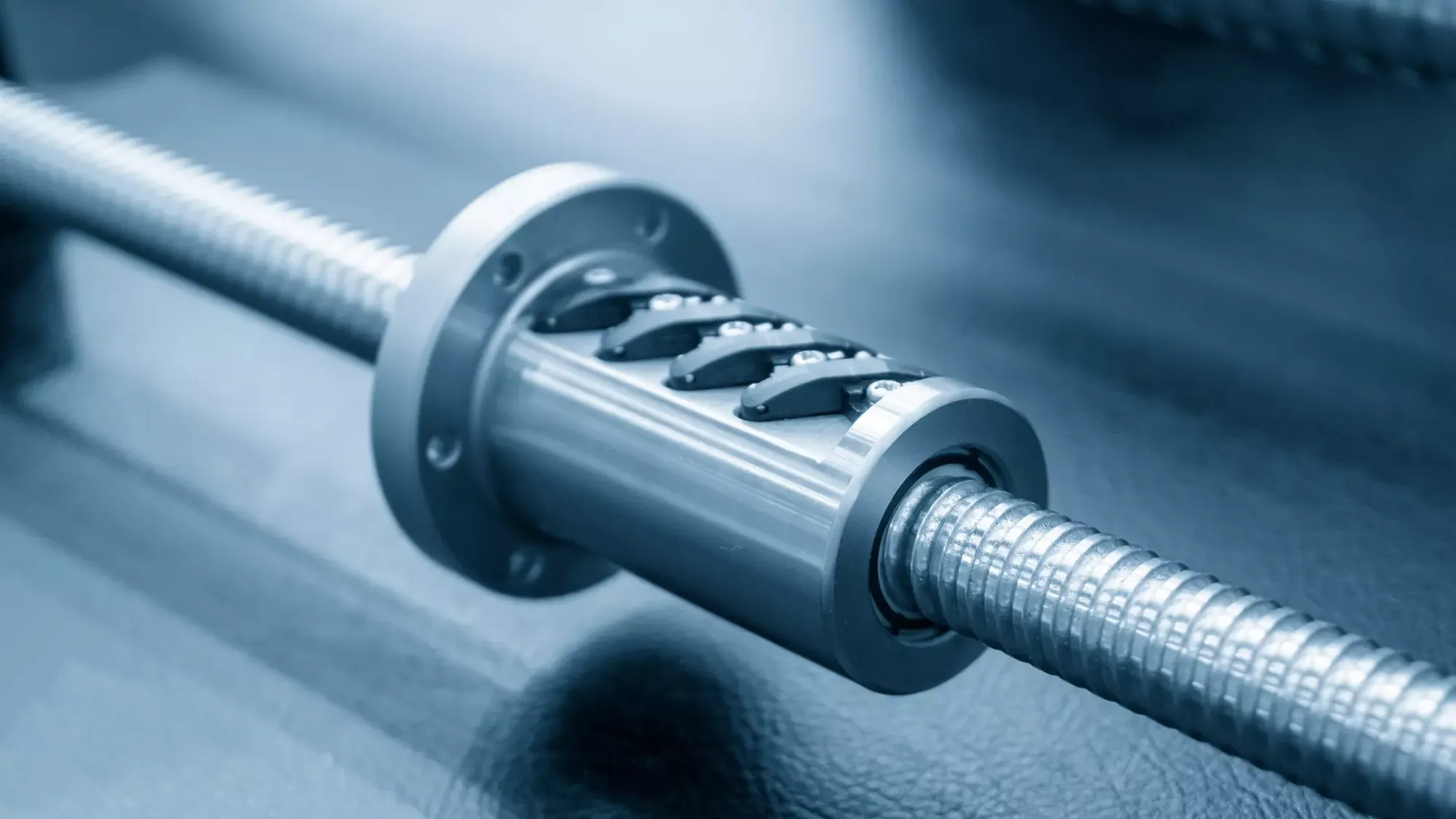
In the intricate and demanding world of CNC machining, the distinction between near-perfection and flawless execution often lies in the nuances. As craftsmen, we deploy sophisticated equipment and techniques to bring our creations to life, and in doing so, accuracy is of paramount importance. Yet, even in this high-tech domain, there lurks an age-old mechanical nemesis known as 'backlash'. This seemingly minor deviation can have significant ramifications, affecting both the quality of the end product and the efficiency of the machining process.
The journey to mastering CNC operations is filled with a myriad of learning curves, and understanding backlash is one of the most pivotal. The good news is, once you know what to look for and how to tackle it, managing backlash becomes a routine aspect of ensuring machine precision. In this guide, I'll walk you through the what, why, and how of backlash, providing hands-on tips to help you detect, prevent, and rectify this challenge, ensuring your CNC machine consistently delivers top-tier results.
Understanding Backlash
Backlash can be understood as the play or movement that exists between two interfaced components, in the absence of any applied force or motion. In CNC terms, it's the difference between the movement you expect from your machine based on your input and the movement you actually get.
Backslash is the difference between the movement you expect from your machine based on your input and the movement you actually get.
Backlash can be found in numerous mechanical systems, but in the context of CNC machining, it's most often associated with the movement interfaces, particularly where rotary motion converts into linear motion. This could be in ball screws, lead screws, gear systems, or any point where two parts move relative to each other.
Imagine a train car. As the engine pulls forward, there's a brief moment where the links between each car tighten before pulling the next car. This momentary slack or gap before the next car moves is akin to the backlash in a CNC machine.
If you were to plot the expected movement of a CNC machine against its actual movement, in a perfect world, both would align perfectly. Backlash introduces a delay or discrepancy.
If you expect an axis to move 10mm, and due to backlash, it only moves 9.8mm, you have a 0.2mm backlash.
In multi-axis CNC systems, backlash in one axis can have compounded effects when combined with other axes. This can lead to complex inaccuracies, especially in intricate 3D milling tasks.
Backlash doesn't just affect the dimensions of the finished product. It can also lead to an uneven finish, especially when the machine changes direction. If the tool doesn't move smoothly due to backlash, the cut or mill can be uneven, leading to surface imperfections.
Consistent, unchecked backlash can lead to premature wear and tear. This is because the constant slack followed by rapid tension can stress components. Over time, this can result in system failures or the need for more frequent maintenance.
Backlash might sound like a minor hiccup, but its effects can ripple through a CNC project, affecting everything from accuracy to the longevity of the machine. As with many challenges in precision engineering, understanding the issue is the first step towards effectively managing and mitigating it.
Why Does Backlash Matter?
In a domain where precision is king, even minor deviations can lead to product rejections or, worse, machine damages. Backlash affects repeatability and overall accuracy of CNC machines. Therefore, understanding and managing backlash becomes paramount for any machinist aspiring for perfection.
1. Precision & Accuracy:
- Dimensional Deviations: Even minimal backlash can introduce errors in the final dimensions of a product. In industries where tight tolerances are a must (like aerospace or medical device manufacturing), even a fraction of a millimeter off can render a part useless.
- Complex Geometries: For intricate designs and detailed projects, backlash can throw off intricate geometric patterns, leading to misalignments.
2. Surface Finish Quality:
- Rough Surfaces: Backlash can create inconsistent movement of the tool, resulting in rough or uneven surfaces, especially during direction changes.
- Chattering: As the tool changes its direction and the backlash is encountered, there can be a chattering effect, leading to imperfections on the part's surface.
3. Tool Life & Wear:
- Increased Wear: Tools might undergo excessive wear if they're subject to irregular movements caused by backlash, meaning you'll have to replace or sharpen them more often.
- Potential Breakage: The sudden jerk or change in motion can sometimes cause fragile tools to break, especially when they're operating at high speeds or under heavy loads.
4. Machine Health & Longevity:
- Accelerated Degradation: Persistent backlash can lead to quicker wear of mechanical components, leading to the need for more frequent repairs or replacements.
- Unexpected Failures: The repetitive stress caused by backlash can sometimes lead to sudden machine failures, which not only disrupt operations but can also be costly to fix.
5. Increased Operational Costs:
- Material Wastage: Parts produced with inaccuracies due to backlash may have to be scrapped, leading to material wastage.
- Time-Consuming: Adjusting for backlash or remanufacturing parts can increase the operational time, thereby reducing the efficiency of the production process.
6. Repeatability Concerns:
- Inconsistent Results: For mass production, repeatability is key. Backlash can introduce variability, meaning that two seemingly identical operations might yield slightly different results.
7. Safety Concerns:
- Unexpected Movements: Especially in larger machines, unexpected movements due to backlash can be a safety concern, posing risks to operators or other equipment nearby.
Backlash isn't just a technical challenge; it's a multifaceted concern that impacts the quality, efficiency, safety, and cost-effectiveness of CNC machining operations. Addressing it is not just about improving the quality of a single product but enhancing the overall reliability and performance of the machining process.
Detecting Backlash
Being able to detect backlash is a crucial skill for any CNC machinist. Just as a doctor's diagnosis informs the treatment, identifying backlash paves the way for its rectification.
1. Visual Inspection:
- Watch the Tool: Pay close attention to the tool, especially during changes in direction. A discernible lag or momentary hesitation often hints at backlash.
- Inspect Movement Transitions: Rapid transitions between operations, such as moving from drilling to milling, can reveal backlash if the tool doesn't align precisely where expected.
2. Dial Indicator Test:
- Setting Up: Attach a dial indicator to the machine's movable part (like the spindle). Zero it out against a fixed point.
- Testing Movement: Move the machine a known distance away and then back again. The dial should return to zero if there's no backlash. Any deviation from zero indicates the magnitude of the backlash.
- Multiple Axis Testing: It's important to repeat this test for each axis since backlash can vary between different machine axes.
3. Cutting Tests:
- Straight Line Test: Machine a straight line, then measure it against the expected dimensions. If there's a discrepancy, it could be due to backlash.
- Circular Test: Milling a circle and then measuring its diameter can reveal backlash, especially if the circle isn't perfectly round or if it's off-center.
- Direction Change Analysis: While machining a pattern that requires multiple changes in direction, observe for uneven cuts or misalignments at the points of change. These are often telltale signs of backlash.
4. Auditory Clues:
- Listen for Chatter: As mentioned earlier, backlash can cause chattering. If you hear inconsistent sounds during operation, it might be backlash at play.
- Identify Irregular Noises: Any unexpected or unusual noises, especially during direction changes, can indicate backlash.
5. Advanced Detection Methods:
- Laser Measurement Systems: These use lasers to accurately measure the movement and position of the machine, comparing the expected versus actual results.
- Ballbar Testing: This method involves using a telescoping bar with precision balls at each end. The machine moves in a circular motion while the ballbar measures the circle's accuracy, providing insights into any mechanical issues like backlash.
6. Feedback from CNC Controllers:
- Error Messages: Modern CNC controllers often come with diagnostic tools that flag inconsistencies. Watch for error messages or warnings related to unexpected tool positions.
- Backlash Compensation Data: Some machines store compensation data to adjust for known amounts of backlash. Periodically reviewing this data can help gauge if backlash is increasing over time.
7. Tactile Feedback:
- Manual Movement: With the machine powered down, manually move the machine components. If you feel a slack or play before components engage, it's indicative of backlash.
- Feeling Vibrations: During operation, excessive vibrations or sudden jolts can be symptoms of backlash, as the tool compensates for the slack.
Regularly checking for backlash is vital for maintaining CNC machine health and ensuring product quality. Just like regular health check-ups can preempt severe illnesses, timely detection of backlash can save time, money, and effort by preventing more significant problems down the road.
Combatting Backlash
Addressing backlash isn't just a reactive step after detection; it's an ongoing commitment to maintaining precision in CNC machining. Equipped with knowledge and the right techniques, you can keep backlash at bay.
1. Regular Maintenance:
- Lubrication: Keeping components well-lubricated reduces wear, ensuring that parts fit together tightly and move smoothly.
- Inspection: Frequently inspect lead screws, nuts, and other interfaced components for signs of wear or damage. This proactive approach allows for timely replacements before significant backlash develops.
- Alignment Checks: Ensure that all components are aligned correctly. Misalignments can not only lead to backlash but also other operational issues.
2. Use Anti-backlash Nuts:
- How They Work: These specially designed nuts employ a combination of springs or wedges to counteract any slack, effectively eliminating backlash.
- Regular Adjustments: Over time, the tension in these nuts may need to be adjusted. Regularly check and recalibrate them to maintain their efficacy.
3. Opt for Ball Screws:
- Precision Movement: Unlike traditional lead screws, ball screws offer a smoother and more accurate movement, reducing the chances of backlash.
- Cost vs. Benefit: While ball screws might have a higher initial cost, the long-term benefits in terms of reduced wear and minimized backlash can make it a worthy investment.
4. Software Compensation:
- Backlash Compensation Features: Many advanced CNC controllers have built-in backlash compensation settings, allowing you to input the known backlash values. The software then adjusts commands to counteract this known error.
- Regular Updates: Ensure that your CNC software is up to date. Manufacturers often release updates that improve compensation algorithms.
5. Mechanical Solutions:
- Dual Nut Systems: These systems use two nuts with opposing threads. The tension between them can eliminate the slack, reducing backlash.
- Preloaded Components: Some machine components are designed with intentional tension or preload, which counteracts the play that causes backlash.
- Rigid Couplings: Replacing flexible couplings with rigid ones can help reduce any slack in the connections, thereby minimizing backlash.
6. Tight Tolerances in Machine Design:
- Precision Components: Invest in high-quality components that are manufactured with tight tolerances. These parts fit together more precisely, leaving less room for play.
- Upgrades: Consider upgrading older components with newer, precision-engineered ones designed specifically to reduce backlash.
7. Training & Best Practices:
- Operational Speed: Sometimes, simply reducing the operational speed of the CNC machine can minimize the effects of backlash.
- Awareness Among Operators: Ensure that all machine operators are well-trained and aware of backlash. Their vigilance can help in early detection and mitigation.
8. Design Considerations:
- Allowing for Backlash: If eliminating all backlash proves too challenging, consider incorporating a small, known amount of backlash and then design parts with this in mind.
- Alternative Paths: Sometimes, simply changing the tool's path can minimize the effects of backlash, especially in areas where direction changes frequently.
The battle against backlash is continuous. By marrying a proactive maintenance approach with strategic mechanical and software solutions, you can ensure that your CNC operations remain precise and efficient. Remember, it's not just about rectifying issues but also about implementing preventive measures to ensure top-notch machine performance consistently.
Regular Monitoring is Key
Once you've implemented these fixes, it's crucial to routinely check for backlash. As your machine ages and components wear down, backlash can reemerge. By keeping a vigilant eye and implementing preventive measures, you can ensure that backlash remains a non-issue.
Closing Thoughts
Backlash, in its sneaky persistence, serves as a timely reminder of the intricacies of CNC machining. It emphasizes that while modern machines are marvels of engineering, they're not immune to the age-old challenges posed by mechanical intricacies. However, with an in-depth understanding, timely detection, strategic combatting methods, and consistent monitoring, it becomes not just manageable but entirely surmountable.
Being proactive in our approach to backlash not only safeguards the accuracy of our current projects but also preserves the longevity and efficiency of our machines for future endeavors. In the ever-evolving world of CNC machining, where precision and consistency are paramount, addressing backlash head-on is a testament to a machinist's dedication to the craft. It's a dance between human ingenuity and machine precision, choreographed to produce the finest outcomes.
If you've found this guide helpful, share it with fellow CNC enthusiasts. After all, in the world of making, knowledge is the tool that sharpens all others! Keep your machine in top shape, continuously refine your skills, and Happy Machining! 🛠️