The Lead Screw Explained: The Backbone of Precision Motion Control
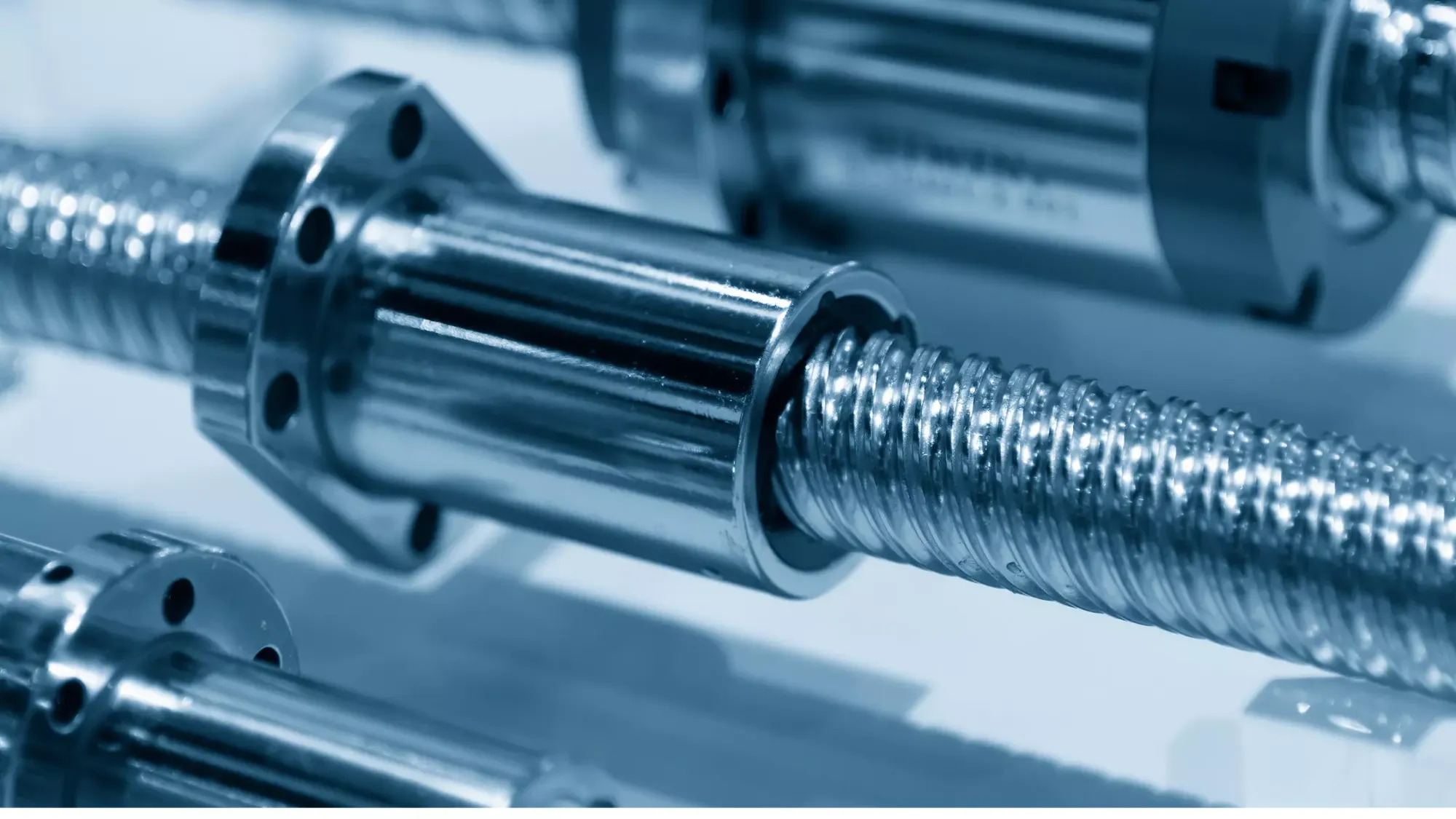
In the intricate ballet of CNC machinery, every component plays a vital role, ensuring the dance of precision and movement unfolds seamlessly. Among these components, the lead screw stands out, a quiet maestro conducting the symphony of accurate, linear motion. Often overlooked by beginners but deeply appreciated by experienced machinists, the lead screw is the unsung hero of the CNC world.
It's the bridge between the motor's rotational energy and the controlled, precise movements we see in CNC outputs, be it intricate carvings or complex assemblies. As we delve deeper into understanding this key component, we'll unravel its importance, its functionality, and the reasons it holds such a revered place in the world of machining.
Lead Screw: The Basics
A lead screw is often described as the backbone of many mechanical systems. At its core, it's a simple concept, but the engineering behind it and its applications are far-reaching. Here's a deeper look into the basics:
1. Anatomy of a Lead Screw:
A lead screw is comprised primarily of two parts: the threaded rod (the screw itself) and a correspondingly threaded nut. The design, pitch, and shape of these threads determine many of the lead screw's functional properties, such as the distance it will move linearly with each rotation (often referred to as its "lead").
2. How it Works:
The fundamental operation is quite straightforward. When the screw rotates, due to the engagement between the threads of the screw and the nut, the nut is propelled in a linear direction. If the nut is prevented from rotating, it will move along the length of the screw; conversely, if the nut is allowed to rotate but prevented from moving linearly, it will cause the screw to move instead.
3. Thread Profile:
The shape and design of the screw's threads are critical. There are multiple thread profiles, with the most common being trapezoidal or square. The profile influences factors such as the lead screw's efficiency, wear rate, and load-carrying capacity.
4. Material Matters:
Lead screws can be made from various materials, including steel, stainless steel, and even brass in some applications. The choice of material will depend on the desired properties. For example, steel lead screws might be preferred for their strength in high-load applications, while stainless steel might be chosen for corrosion resistance in certain environments.
5. Efficiency & Friction:
One of the key aspects of a lead screw's design is its efficiency. The nature of the contact between the screw and the nut generates friction. This friction can be both beneficial and a challenge. On the one hand, it can prevent back-driving (where the load pushes back on the screw). On the other hand, it can lead to wear and reduced efficiency. This is one reason why variations like ball lead screws, which use ball bearings to reduce friction, were developed.
6. Pitch vs. Lead:
While these terms are often used interchangeably, there's a distinction. The pitch refers to the distance between the threads, while the lead is the linear distance the nut will move with one full rotation of the screw. In single start screws (one continuous thread), the pitch and lead are the same. However, in multi-start screws (multiple threads running parallel), the lead is the product of the pitch and the number of starts.
Understanding these foundational elements of lead screws helps users and makers make informed decisions about their design, maintenance, and application in their projects. Whether one is designing a new machine or looking to optimize an existing setup, knowledge about the basics of lead screws becomes pivotal.
The Role in CNC Machines
When we talk about CNC (Computer Numerical Control) machines, we often focus on their digital aspects, like software, programming, or control systems. Yet, the unsung heroes ensuring these virtual commands get flawlessly translated into real-world precision are the mechanical components, with the lead screw taking center stage. Let's delve deeper into its role in CNC machines:
1. Motion Control:
At the heart of a CNC machine's operation is the need for exact movement. The lead screw's primary responsibility is to provide controlled and repeatable linear motion. As the computer sends commands, the lead screw ensures the machine's physical parts move to the precise location specified, down to minute accuracies.
2. Precision and Accuracy:
The very essence of CNC machining is high precision. The lead screw’s design, from its thread profile to its material, plays a direct role in ensuring the tool head or workpiece moves with pinpoint accuracy. The consistency and tight tolerances of a well-manufactured lead screw ensure that designs are replicated flawlessly, whether it’s the first or thousandth piece being machined.
3. Translating Rotational to Linear Motion:
CNC motors produce rotational motion. However, for tasks like carving, drilling, or milling, linear movement is needed. The lead screw acts as a translator, converting the motor's rotational energy into the exact linear motion required by the tool head.
4. Multi-axis Coordination:
Most advanced CNC machines work on multiple axes (X, Y, Z, and even more in some cases). Each axis will typically have its own lead screw. The simultaneous and coordinated movement of these screws is what allows for intricate designs, curves, and patterns, bringing multi-dimensional creations to life.
5. Load Management:
CNC machines can work with a variety of materials, from soft plastics to hard metals. The resistance or feedback from these materials can vary. The lead screw, being robust and durable, ensures that the machine can handle different loads, be it from the material being carved or the force exerted by the tool itself.
6. Backlash Management:
Backlash, or the slight play between the threads of the lead screw and its nut, can be a challenge in maintaining precision. High-quality CNC systems often incorporate anti-backlash nuts or similar mechanisms to ensure that this play doesn't affect the final output's accuracy.
7. Speed Variability:
Not all machining operations require the same speed. Some might need slow, deliberate cuts, while others might be suited for faster passes. The lead screw, in conjunction with the machine's control system, allows for this variable speed, ensuring that the machine operates optimally for the task at hand.
While a CNC machine is a symphony of numerous components working in harmony, the lead screw is undeniably one of its principal players. It bridges the gap between digital precision and mechanical execution, ensuring that what's designed on a computer screen manifests accurately in the real world.
Types of Lead Screws
Lead screws have been instrumental in the design and functionality of a myriad of machines. Yet, it's not a 'one-size-fits-all' scenario. Depending on the specific application, desired efficiency, load-bearing capability, and other factors, different types of lead screws have been developed.
Let's dive into a more detailed exploration:
1. Acme Lead Screws:
- Profile: Characterized by their trapezoidal thread shape, Acme lead screws are one of the most commonly used varieties, mainly because of their blend of efficiency and strength.
- Advantages: Their design provides robust engagement between the screw and the nut, resulting in reliable power transmission and durability.
- Applications: Due to their balance of strength and cost-efficiency, they're found in a range of applications, from CNC machines to lifting mechanisms.
2. Ball Lead Screws:
- Profile: Unlike the direct thread-to-thread contact in traditional lead screws, ball lead screws use circulating ball bearings that ride between the threads of the screw and the nut.
- Advantages: This ball-bearing mechanism significantly reduces friction, providing higher efficiency, less wear, and a longer lifespan. It also allows for smoother, more precise motion.
- Drawbacks: They can be more expensive than other types and might require a more complex maintenance routine due to the ball recirculation system.
- Applications: Commonly used in scenarios demanding high precision and efficiency, like in high-end CNC machinery, robotics, and aerospace applications.
3. Roller Lead Screws:
- Profile: These screws use roller bearings, which, like the ball lead screws, ride between the screw and the nut threads.
- Advantages: Roller lead screws strike a balance between ball screws and traditional threaded designs. They offer reduced friction (though generally more than ball screws) and can bear higher loads than ball screws.
- Drawbacks: They might not offer the same level of precision as ball screws, but they usually outperform Acme screws in this respect.
- Applications: Suitable for applications that need a balance between efficiency and load-bearing capacity, such as industrial automation and some CNC machines.
4. Square Thread Lead Screws:
- Profile: As the name suggests, these screws have a square-shaped thread profile.
- Advantages: Offering minimal friction due to their profile, they're efficient and can handle high loads. However, they are more challenging and expensive to manufacture compared to trapezoidal threads.
- Applications: Used in specific scenarios where high power transmission is needed, like in jacks or large machinery.
5. Multi-start Lead Screws:
- Profile: These screws have multiple threads running parallel, which means they have several entry points or "starts."
- Advantages: A multi-start screw moves the nut faster for each rotation (higher lead) without changing the pitch. This allows for quicker linear movement without compromising on thread strength.
- Applications: Useful in scenarios where rapid movement is necessary without losing the advantages of a finer pitch.
While the foundational principle of lead screws remains consistent, the various types have been engineered to cater to specific requirements. This diversity ensures that whether it's the delicate operation of a 3D printer or the heavy-duty demands of an industrial press, there's a lead screw tailored for the job.
Practical Aspects for Makers:
For makers, tinkerers, and DIY enthusiasts, understanding the theoretical aspects of lead screws is only half the battle. Practical knowledge is crucial when it comes to making informed decisions for projects. Whether you're crafting a CNC router from scratch, designing a linear actuator for a unique application, or merely tinkering with a novel invention, the nuances of lead screws can make a significant difference. Here’s a hands-on guide for those on the creative front:
1. Selecting the Right Lead Screw:
- Purpose & Precision: The first step is understanding your project's needs. If you’re building a 3D printer or a CNC machine, precision is paramount, making ball lead screws a viable choice. For heavier-duty applications with less need for minute accuracy, Acme or roller screws might be more suitable.
- Budgetary Considerations: While ball lead screws offer unparalleled precision, they can be pricey. Assessing your budget can help narrow down your choices. Remember, in some cases, a well-maintained and appropriately chosen Acme screw might serve just as well.
2. Maintenance Matters:
- Lubrication: Regularly lubricating your lead screw can enhance its performance and lifespan. The type of lubricant can vary based on the screw type and application. For instance, Teflon-based lubricants might be excellent for high-speed applications.
- Dust and Debris: Especially in woodworking CNCs or environments with particulates, ensure your lead screw is protected or regularly cleaned. Accumulated debris can affect precision and cause wear.
3. Integration with Motors:
- Matching Specifications: When connecting your lead screw to a motor, ensure that the motor's torque and speed align with the lead screw's requirements. Too much torque might cause unnecessary wear, while too little can result in poor performance.
- Couplings: Use high-quality couplings to connect the lead screw to the motor. This ensures smooth energy transfer and reduces the chances of misalignment or wobbling.
4. Addressing Backlash:
- Anti-backlash Nuts: These are essential for applications demanding high precision. They reduce the play between the screw and the nut, ensuring movement consistency.
- Regular Calibration: Periodically check for backlash, especially if you notice any discrepancies in your output. Calibrating your setup can rectify minor issues before they escalate.
5. Experimentation is Key:
- Test Runs: Before finalizing any setup, always run multiple tests. Check for movement accuracy, potential obstructions, and ensure all parts, not just the lead screw, work harmoniously.
- Iterative Learning: Every project can offer new insights. Perhaps a certain lead screw type works unexpectedly well for an unconventional application. Document your observations, and don’t be afraid to iterate and tweak.
6. Join the Community:
- Forums & Groups: There are countless online forums and maker communities where individuals share their experiences, insights, and challenges related to lead screws and other components.
- Collaborative Learning: By participating in discussions, asking questions, and sharing your own findings, you not only enrich your knowledge but also contribute to the collective wisdom of the maker community.
The world of lead screws, while technical, is immensely rewarding when navigated with a mix of informed decision-making and hands-on experimentation. Each project offers a canvas for makers to explore, learn, and most importantly, create with confidence.
Conclusion
In the vast panorama of mechanical components, lead screws emerge as both foundational and transformative. Their intricate designs and variations serve as the backbone for numerous devices and creations. While understanding their technicalities is crucial, the true magic lies in the application — where theoretical knowledge is shaped, molded, and transformed into tangible innovation. Every twist, turn, and rotation of a lead screw can bring a creator's vision one step closer to reality, emphasizing their undeniable significance in the realm of mechanical design.
For makers, this is an open invitation to dive deep, to experiment, and to constantly refine their craft. Every project undertaken provides a unique learning experience, a lesson in both the art of creation and the science of precision. By embracing the dualities of theory and practice, and the interplay of knowledge and hands-on application, makers don't just create; they evolve, pushing the boundaries of what's possible. In this journey, lead screws aren't just tools; they're trusted companions, guiding each endeavor toward perfection.
Happy Machining! 🛠️