Canned Cycles in CNC Machining: A Practical Guide
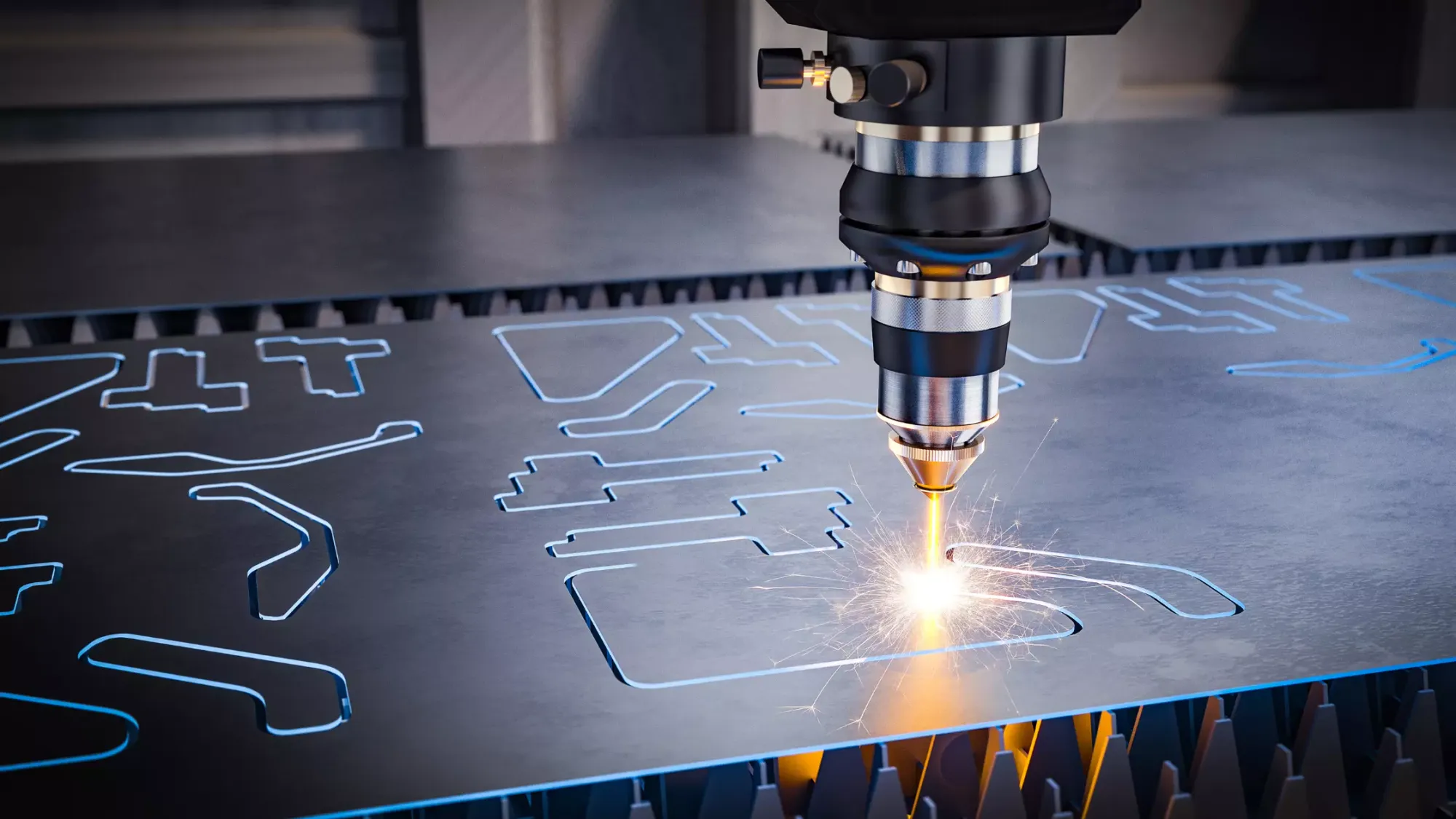
One concept that often piques the curiosity of both budding and seasoned machinists is the "canned cycle." At a glance, the term might sound like something straight out of a food processing unit, but in the world of computer numerical control, it holds a significance that can't be overlooked.
Canned cycles represent the epitome of efficiency in CNC programming. They serve as predefined sequences, allowing machinists to execute a series of operations with a single code, eliminating the need to input each movement manually. This not only streamlines the machining process but also ensures precision and consistency. As we delve deeper into this topic, we'll uncover the practical aspects of canned cycles and how they've revolutionized CNC operations.
Understanding Canned Cycles
Canned cycles, in the context of CNC machining, can be visualized as the "macros" or "shortcuts" of the machining world. Just as a computer macro allows a user to perform multiple tasks with a single command, a canned cycle lets a machinist execute a series of intricate machine operations using a singular, predefined code. This concept is rooted in the idea of simplifying complex procedures, making them more accessible and efficient.
Canned cycles are not just about simplification; they're about standardization.
At a foundational level, a canned cycle is designed to reduce the volume of G-code a programmer has to write. G-code, the language of CNC machines, dictates every movement and function of the machine. For repetitive tasks, writing out each line of G-code can be tedious and error-prone. Enter canned cycles, which encapsulate these repetitive sequences into a single command. For instance, instead of programming every step of a drilling operation – from the approach, penetration, to retraction – a machinist can use a drilling canned cycle with specific parameters to achieve the desired result.
Moreover, canned cycles are not just about simplification; they're about standardization. By using them, machinists ensure that specific operations are carried out the same way every time, leading to consistent and predictable results. This standardization is crucial in industries where precision and repeatability are paramount, such as aerospace or medical device manufacturing.
Another noteworthy aspect is the adaptability of canned cycles. While they are predefined, many modern CNC machines allow machinists to modify or adjust certain parameters within a canned cycle. This flexibility ensures that while the core operations remain standardized, there's room for customization based on the unique requirements of a project.
Understanding canned cycles is akin to understanding the balance between automation and control in CNC machining. They offer machinists a tool to automate repetitive tasks while still retaining the ability to fine-tune operations to meet specific needs. As CNC technology continues to advance, the role and capabilities of canned cycles are likely to expand, further cementing their importance in the machining process.
Why Use Canned Cycles?
The utilization of canned cycles in CNC machining is not just a matter of convenience; it's a strategic approach to enhance productivity, accuracy, and overall machining efficiency.
- Streamlined Programming: One of the primary advantages of canned cycles is the drastic reduction in programming time. Instead of manually inputting every single command for a repetitive operation, machinists can rely on a single canned cycle. This not only speeds up the programming process but also makes the code more readable and manageable.
- Reduced Margin for Error: Manual programming, especially for intricate and repetitive tasks, opens the door for human errors. A simple oversight can lead to costly mistakes. Canned cycles, by encapsulating complex sequences into standardized codes, minimize the chances of such errors, ensuring that operations are carried out correctly every time.
- Consistent Results: In industries where precision is non-negotiable, consistency is king. Canned cycles guarantee that a specific operation, whether it's drilling or tapping, is executed in the same manner each time. This uniformity ensures that every produced part meets the set standards, eliminating variability in the production process.
- Optimized Machine Operations: Canned cycles are often designed with optimization in mind. They can automatically adjust certain parameters, such as feed rate or spindle speed, based on the operation's requirements. This ensures that the machine operates at its optimal efficiency, leading to faster production times and reduced wear and tear on the machine.
- Flexibility and Customization: While canned cycles are predefined sequences, they are not rigid. Modern CNC systems allow machinists to tweak various parameters within a canned cycle, offering a balance between standardization and customization. This adaptability ensures that machinists can cater to the unique requirements of each project without compromising the benefits of using canned cycles.
- Enhanced Learning Curve: For newcomers to the CNC world, understanding and mastering G-code can be daunting. Canned cycles simplify this learning process. By familiarizing themselves with the most common canned cycles, beginners can quickly start producing parts without delving deep into the intricacies of manual programming.
The question isn't so much "Why use canned cycles?" but rather "Why not?" They represent a fusion of efficiency, precision, and adaptability, making them an invaluable tool in the arsenal of every CNC machinist. Whether you're aiming for rapid production, unmatched precision, or a blend of both, canned cycles pave the way for machining excellence.
Common Types of Canned Cycles
Canned cycles have become an integral part of CNC machining, offering a range of predefined sequences tailored for specific operations. By understanding the various types of canned cycles available, machinists can better harness their capabilities and optimize their machining processes.
Drilling Cycles:
- Standard Drilling: This is the most basic form of drilling cycle, used for creating holes in a workpiece. The machine is programmed to approach the material, drill to a specified depth, and then retract.
- Deep Hole Drilling (Peck Drilling): Designed for drilling deeper holes, this cycle involves the drill bit making successive "pecks" into the material, retracting slightly between each peck to remove chips and prevent tool binding or breaking.
- Counterboring: This cycle is used to enlarge a hole to a specific diameter and depth, typically to accommodate a bolt head or screw.
Boring Cycles:
- Precision Boring: Used when a hole needs to be finished to a tighter tolerance than what drilling can achieve. The tool incrementally removes material to achieve the desired diameter and finish.
- Back Boring: This cycle allows for boring the backside of a hole, ensuring both ends of a hole have precise dimensions.
Tapping Cycles:
- Rigid Tapping: A synchronized tapping process where the spindle rotation and feed are coordinated to match the thread pitch. This ensures precise thread formation without the need for floating tap holders.
- Non-Rigid Tapping: Unlike rigid tapping, this cycle uses a compression/tension tap holder to compensate for minor synchronization errors between the spindle rotation and feed.
Facing Cycles:
- Standard Facing: This cycle is designed to remove material from the surface of a workpiece to achieve a flat finish. The tool moves in a predefined pattern, ensuring an even surface.
- Contour Facing: Used for surfaces that aren't flat, this cycle allows the tool to move in a pattern that follows the contours of the workpiece, ensuring a smooth finish.
Grooving Cycles:
- External Grooving: This cycle is used to cut grooves on the outer surface of a workpiece, often for applications like O-ring seats or keyways.
- Internal Grooving: Similar to external grooving but focused on the inner surfaces, this cycle is used for creating grooves inside bores or other internal features.
Thread Milling Cycles:
- Used for producing threads using a rotating tool, this cycle offers an alternative to traditional tapping. It's especially useful for producing large threads or threads in hard materials.
The variety of canned cycles available reflects the diverse range of operations that CNC machines are capable of. By leveraging these predefined sequences, machinists can achieve precise results in a fraction of the time it would take with manual programming. As CNC technology continues to evolve, we can expect even more specialized canned cycles to emerge, further enhancing the capabilities of modern machining.
Practical Tips for Using Canned Cycles
Canned cycles, while designed to simplify and streamline CNC operations, still require a thoughtful approach to ensure they're utilized to their fullest potential. Whether you're a seasoned machinist or a newcomer to the CNC world, adhering to best practices can make a significant difference in the outcome of your projects.
- Thoroughly Understand the Cycle: Before implementing any canned cycle, take the time to fully understand its parameters and functions. Each machine and control system might have slight variations in how they interpret and execute canned cycles. Familiarizing yourself with the specifics can prevent unexpected results.
- Always Double-Check Parameters: A canned cycle's efficiency lies in its predefined sequence, but the parameters you input dictate its behavior. Always ensure that values like depth, diameter, and feed rate are accurate for the material and operation at hand.
- Use Simulation Features: Many modern CNC machines come equipped with simulation features that allow you to visualize the operation before actual machining. This can help identify potential collisions, errors, or inefficiencies in the canned cycle.
- Stay Updated with Machine Manuals: Machine manufacturers often release updates or revisions to their manuals, which might include new canned cycles or modifications to existing ones. Regularly reviewing these manuals ensures you're leveraging the most up-to-date and optimized cycles.
- Prioritize Tool and Workpiece Safety: While canned cycles are designed for efficiency, never compromise on safety. Ensure that tools are in good condition and that workpieces are securely clamped. A slight oversight can lead to tool breakage or workpiece damage.
- Opt for Custom Cycles When Necessary: While standard canned cycles cover a wide range of operations, there might be instances where a custom cycle is more appropriate. Some CNC systems allow users to create and save their own canned cycles tailored to specific tasks.
- Document and Annotate: Especially when working with complex projects, it's beneficial to annotate your program. Clearly document which canned cycles are used, their parameters, and any modifications made. This not only aids in troubleshooting but also makes it easier for others to understand the program.
- Regularly Test and Calibrate: Over time, machine wear and tool degradation can affect the outcome of canned cycles. Regularly testing and calibrating your machine ensures that the results of the canned cycles remain consistent and accurate.
- Engage with the CNC Community: The CNC community is vast and active, with many forums and groups dedicated to sharing knowledge. Engaging with fellow machinists can provide insights into best practices, tips, and tricks for effectively using canned cycles.
- Continuous Learning: The world of CNC is ever-evolving, with new techniques and technologies emerging regularly. Dedicate time to continuous learning, exploring new canned cycles, and refining your skills.
Canned cycles offer a powerful toolset for CNC machinists. Their effectiveness is amplified when used thoughtfully and strategically. By adhering to these practical tips, machinists can ensure that they're harnessing the full potential of canned cycles, leading to impeccable results with every project.
Conclusion
In the ever-evolving landscape of CNC machining, embracing tools like canned cycles is not just a luxury but a necessity. They encapsulate the essence of modern machining, where precision, efficiency, and consistency are intertwined. By leveraging these predefined sequences, machinists can navigate complex projects with ease, ensuring that the end product is of the highest quality, all while saving valuable time and resources.
As we reflect on the significance of canned cycles, it's evident that they are more than just codes in a program. They are a testament to the advancements in CNC technology, bridging the gap between intricate manual operations and automated excellence. Whether you're a novice just starting your journey or a seasoned expert, understanding and utilizing canned cycles will undoubtedly elevate your machining prowess to new heights.