Guide to Crafting with Glass
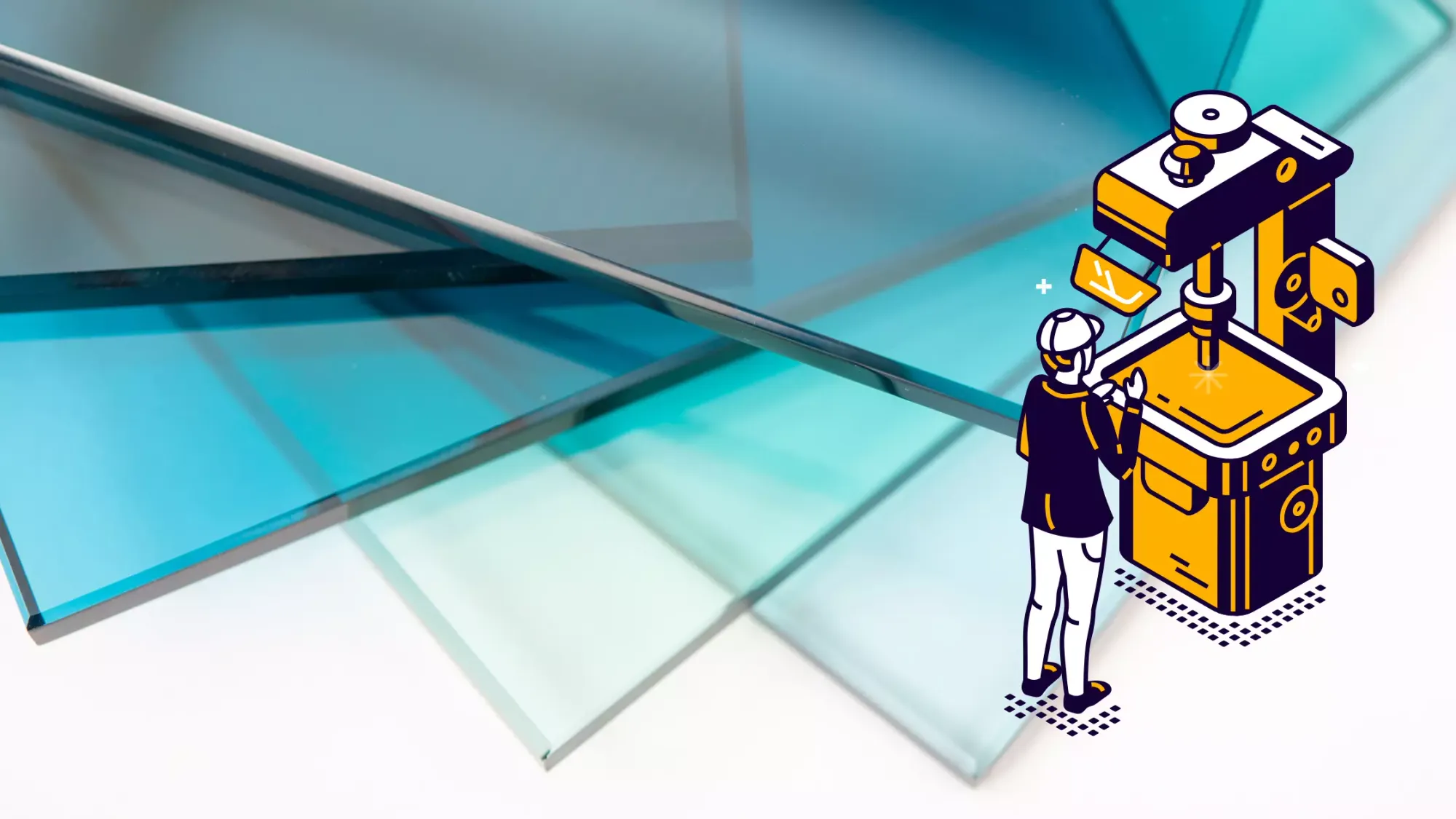
Milling, a well-established technique in the world of manufacturing, has traditionally been associated with metals, woods, and plastics. But what happens when this age-old technique meets the delicate and ethereal world of glass? Glass, a material synonymous with fragility and elegance, presents a unique set of challenges and rewards for those daring enough to shape it using milling.
As we venture into the intricate dance of CNC machines and glass sheets, we uncover a realm where precision meets artistry. Here, patience is the key to unlocking breathtaking designs. Join us as we delve into the mesmerizing world of glass milling, exploring its nuances, challenges, and the sheer magic it can produce.
Safety during glass milling is of utmost importance due to the delicate nature of glass and the potential hazards of the milling process.
Why Mill Glass?
Glass has been used in art, architecture, and everyday items for centuries. Its unique properties make it a sought-after material for various projects. Milling glass allows for precision cuts, intricate designs, and a polished finish that's hard to achieve with other methods.
Aesthetic and Design Flexibility
Milling glass opens up a world of design possibilities that are hard to achieve with other materials.
- Unique Designs: Milling allows for intricate and bespoke designs, transforming ordinary glass into art pieces or functional designs with a touch of elegance.
- Precision: CNC milling offers unparalleled precision, enabling the creation of complex patterns, logos, and detailed engravings on glass surfaces.
- Texture Variations: Beyond just visual designs, milling can introduce various textures to the glass, enhancing its tactile feel and appearance.
Functional Benefits of Glass Milling
Beyond aesthetics, milled glass offers several functional advantages.
- Custom Fittings: Milling allows for precise cuts, ensuring that glass pieces fit perfectly in custom spaces or fixtures.
- Enhanced Safety: Milled edges can be smoothened to reduce the risk of injuries from sharp edges, making the glass safer for various applications.
- Specialized Applications: From creating slots for LED lights to making openings for hardware fittings, milling equips glass for specific functional roles in diverse projects.
The decision to mill glass goes beyond its sheer beauty. It's about pushing the boundaries of what's possible, innovating for the future, and creating pieces that hold both functional and symbolic value. Whether for artistic expression, technological advancement, or economic benefit, milling glass stands as a testament to human ingenuity and the endless possibilities that arise when we challenge the status quo.
Choosing the Right Glass
Not all glass is created equal. For milling, it's crucial to select a type that can withstand the process without shattering. Tempered or laminated glass is often recommended due to its strength and durability.
Types of Glass for Milling:
Selecting the appropriate type of glass is paramount to the success of your milling project.
- Annealed Glass: Often chosen for its ease of cutting, annealed glass is a standard type that hasn't been thermally strengthened. It's ideal for projects that don't require high strength.
- Tempered Glass: This is heat-treated for added strength, making it more resistant to breakage. However, it's crucial to note that once tempered, the glass cannot be cut or milled without shattering.
- Laminated Glass: Comprising two or more glass layers with an interlayer in between, this type offers enhanced safety. The interlayer holds the glass together if it's shattered.
Considerations in Glass Selection:
Beyond the basic type, several factors influence the choice of glass for milling.
- Thickness: Depending on the project, the glass thickness can vary. Thicker glass offers more strength but requires adjustments in milling speed and depth.
- Tint and Coating: Some projects may require tinted or coated glass. It's essential to ensure that the milling process doesn't compromise these features.
- End Use: The final application of the milled glass, whether it's for decorative purposes, structural use, or safety applications, will guide the selection process.
Choosing the right glass for milling is a multifaceted decision that requires a thorough understanding of both the material's properties and the project's requirements. By giving due consideration to the factors mentioned above, one can ensure not only the success of the milling process but also the durability and beauty of the finished product.
Tools of the Trade
The tools used in the milling of glass are pivotal in determining the quality, precision, and safety of the final product.
Essential Tools for Glass Milling
When milling glass, the choice of tools can make a significant difference in the outcome.
- Diamond-Tipped Tools: These are the gold standard for glass milling. Their hardness ensures precision and reduces the risk of chipping.
- Coolant Dispensers: Given glass's sensitivity to heat, a consistent coolant flow is vital. Coolant dispensers help in maintaining the temperature and ensuring smooth cuts.
- Specialized Drill Bits: For drilling holes in glass, it's crucial to use drill bits specifically designed for the material to prevent cracks or breaks.
Tool Maintenance and Safety
The longevity and efficiency of your tools are as crucial as their initial selection.
- Regular Inspection: Tools should be regularly checked for wear and tear. A worn-out tool can lead to imprecise cuts or even damage the glass.
- Proper Storage: Store tools in a dry, cool place and ensure they are cleaned after each use. This not only prolongs their life but also ensures consistent performance.
- Safety First: Always ensure that tools are securely attached to the machine. Loose tools can be a hazard, leading to accidents or damage to the glass.
The tools used in glass milling are a blend of modern technology and time-tested techniques. Each tool plays a crucial role in ensuring that the milling process is efficient, precise, and safe. Investing in high-quality tools and understanding their proper usage is paramount for anyone venturing into the intricate world of glass milling.
Setting Up Your Machine:
Setting up your machine correctly is a critical step in the glass milling process. Proper setup ensures precision, safety, and optimal results.
Machine Calibration and Setup:
Before initiating the milling process, it's crucial to ensure your CNC machine is optimally set up for glass.
- Stability: Ensure the machine is on a stable surface to prevent any vibrations, which can lead to imprecise cuts or even glass breakage.
- Alignment: Double-check the alignment of all machine components. Misalignment can cause uneven pressure on the glass, increasing the risk of cracks.
- Workholding: Use specialized clamps or fixtures designed for glass. This ensures the glass is held securely without introducing undue stress, which can lead to breakage.
Software and Feed Rates
The software settings and feed rates play a pivotal role in the success of the milling process.
- Software Settings: Use software settings tailored for glass milling. This often includes slower speeds and specific tool paths to prevent chipping.
- Feed Rate: Adjust the feed rate to suit the type and thickness of the glass. A slower feed rate is generally recommended to prevent chipping and ensure a smooth finish.
- Depth of Cut: For glass, it's advisable to opt for multiple shallow passes rather than deep cuts. This approach minimizes the risk of cracking or breaking the material.
Setting up your machine for glass milling is a meticulous process that requires attention to detail. Each step, from calibration to safety measures, plays a crucial role in ensuring a successful milling operation. By investing time in proper setup, you not only ensure the longevity of your machine and tools but also guarantee the best possible results in your glass milling projects.
The Milling Process
The milling process of glass is a delicate balance of precision, technique, and patience.
Milling Preparation
Before diving into the actual milling, it's essential to set the stage for a successful process.
- Glass Selection: Opt for a glass type suitable for your project, considering factors like thickness and durability. Annealed glass, for instance, is often preferred for its ease of cutting.
- Design Precision: Ensure your design is precise, with clear guidelines. This is crucial as glass doesn't afford the luxury of mistakes like some other materials.
- Tool Selection: Use tools specifically designed for glass milling. Diamond-tipped tools are often the go-to choice due to their hardness and precision.
The Milling Process
Once everything is set, the actual milling can commence.
- Coolant Use: Always use a coolant during the milling process. This prevents the glass from overheating, which can lead to cracks or breaks. It also aids in achieving smoother cuts.
- Feed Rate: Maintain a consistent and appropriate feed rate. Going too fast can cause chipping, while too slow can generate excessive heat.
- Depth of Cut: It's advisable to make shallower passes when milling glass. Multiple light passes are better than a single deep one, reducing the risk of breakage.
The glass milling process is a journey from conceptual design to a tangible piece of art or utility. Each step requires careful consideration and expertise. While the process can be time-consuming and demands attention to detail, the end result—a beautifully milled piece of glass—is often well worth the effort.
Post-Milling Tips
Once the milling process is complete, there are several post-milling practices and tips that can enhance the final product's quality, safety, and longevity.
Post-Milling Care:
- Cleaning: Use soft brushes or compressed air to remove glass dust and particles.
- Edge Finishing: Smooth sharp edges with diamond hand pads or grinding machines, and polish for a refined look.
- Surface Polishing: Utilize diamond polishing pads for a clear finish and buff with a soft cloth for added shine.
- Documentation: Maintain notes on specific settings, tools, and techniques for future reference.
Storage and Safety:
- Safe Storage: Place on a padded surface or store larger pieces vertically with edge protectors.
- Handling: Always be cautious of sharp edges and handle milled glass with care.
- Protective Gear: Wear appropriate safety equipment, such as gloves and safety glasses, when handling or working near milled glass.
Post-milling practices are as crucial as the milling process itself. They ensure that the final product is not only aesthetically pleasing but also safe and durable. By dedicating time and attention to these post-milling steps, you can elevate the quality of your work and achieve a higher level of craftsmanship in glass milling.
Safety First
Safety during glass milling is of utmost importance due to the delicate nature of glass and the potential hazards of the milling process. Personal Protective Equipment (PPE) is essential: safety glasses shield the eyes from flying glass particles, cut-resistant gloves protect hands from sharp edges, and dust masks prevent inhalation of harmful glass dust. Ensuring the CNC machine's emergency stop is functional and within reach allows for immediate shutdown during anomalies, while safety shields or doors, if present, should always be closed to guard against flying debris. Properly securing the glass to prevent movement during milling is crucial, but care should be taken to avoid over-tightening, which can introduce stress and lead to cracks.
Regular inspection of milling tools ensures they are free from damage and adequately sharp, as dull or damaged tools can cause chipping or overheating. The consistent flow of coolant is vital to prevent the glass from overheating and cracking, but pooling should be avoided to prevent slippage. Proper lifting techniques and the use of edge protectors during storage can prevent accidental breakages. Lastly, ensuring that all operators are well-trained in both machine operation and safety protocols, coupled with prominently displayed safety signage, reinforces the importance of safety precautions and practices in the milling environment.
Conclusions
The art of milling glass is a testament to the incredible advancements in manufacturing and the boundless creativity of artisans. By merging the precision of CNC machinery with the delicate nature of glass, we open up a world of possibilities, allowing for intricate designs and impeccable craftsmanship. This union of technology and artistry not only challenges our conventional understanding of what's possible but also paves the way for innovations that were once deemed unattainable.
In embracing the challenges and intricacies of glass milling, we are reminded of the importance of patience, precision, and passion. As we continue to push the boundaries of what can be achieved, it's essential to approach each project with an open mind and a willingness to learn. The journey of glass milling, with its highs and lows, ultimately leads to creations that are as breathtaking as they are unique, showcasing the true potential of human ingenuity and technological advancement.