Guide to Using Nema 23 Stepper Motors
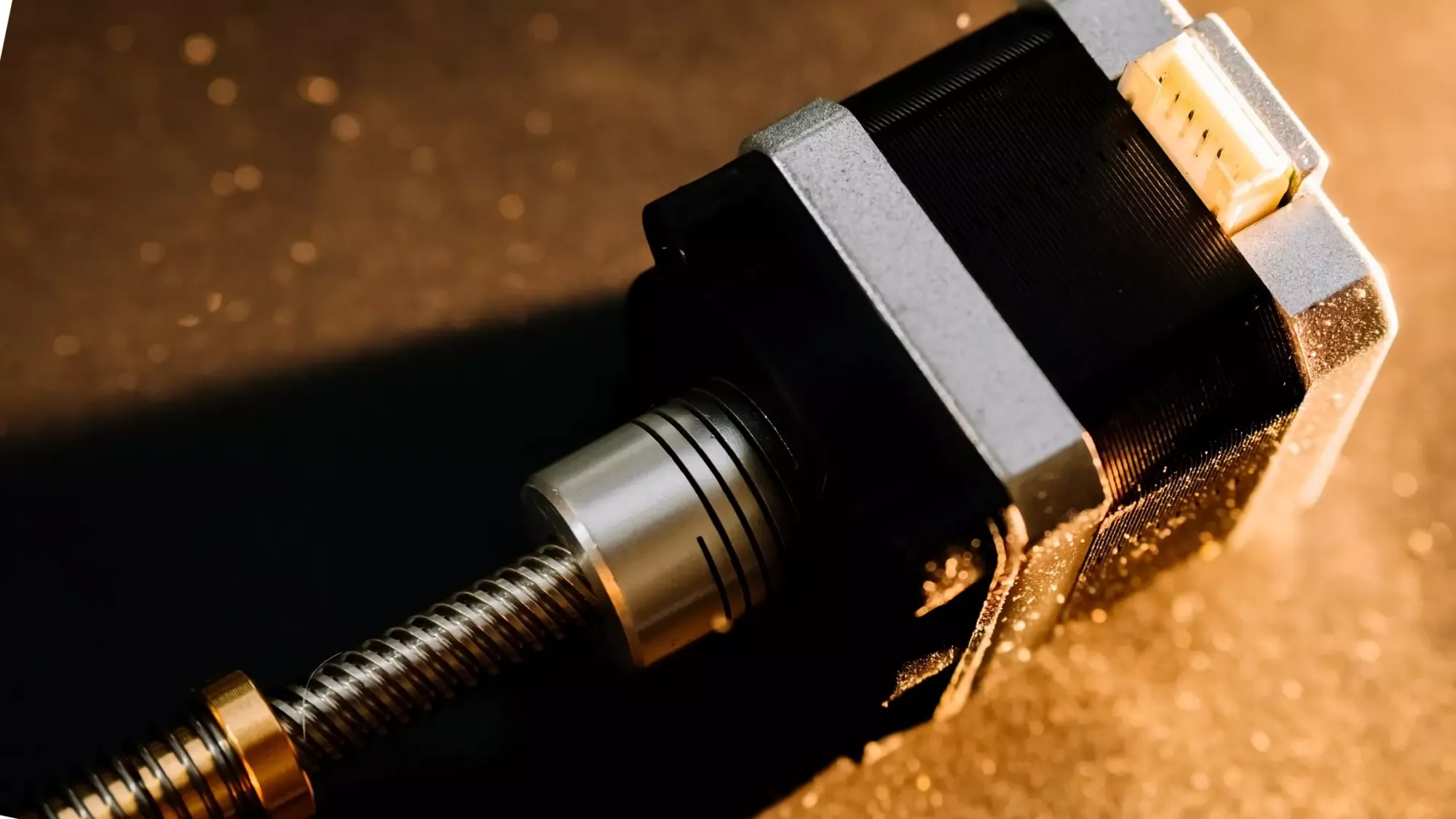
The world of CNC machining is both vast and intricate, a blend of technological advancements and age-old mechanical principles. Every part of a CNC machine has a role to play, a contribution to make to the final result - from the sturdy frame to the tiniest screw. Yet, few components have as direct an impact on the precision and reliability of operations as the stepper motors do.
Enter the Nema 23 stepper motor: a favorite among makers, hobbyists, and professionals. While it might just seem like another component on a spec sheet, it truly is a linchpin in the world of controlled mechanical movement. Today, we will dive deep into the fascinating realm of Nema 23 stepper motors, offering a comprehensive guide to understanding and effectively harnessing them for your projects.
What is a Nema 23 Stepper Motor?
Nema 23 is not just a term but a standard that categorizes stepper motors by their faceplate dimensions. In essence, the '23' in Nema 23 represents the face size of the motor in tenths of inches, translating to approximately 2.3 inches or 58.4 mm. This standardization allows users to easily identify and replace motors in CNC setups, robotics, or other applications without much guesswork.
The '23' in Nema 23 represents the face size of the motor in tenths of inches, translating to approximately dimensions 2.3 inches or 58.4 mm.
But there's more to the Nema 23 than just its size. Stepper motors, as a category, operate differently from typical DC or AC motors. Instead of a continuous rotation, they move in discrete steps, offering unparalleled precision. This "stepping" nature is achieved through internal toothed electromagnets that are sequentially energized, causing the motor's shaft to rotate in set increments.
Nema 23 motors typically stand out for their optimal blend of power and precision. They fill the gap between smaller motors, like the Nema 17, which may not have the required torque for more demanding tasks, and larger motors that might be overkill for medium-duty applications. As such, the Nema 23 finds its sweet spot in projects that require a tad more oomph without escalating to industrial-sized solutions.
Furthermore, the construction of a Nema 23 stepper motor is geared towards longevity and consistency. Encased within its robust exterior are copper windings, which, when energized, create magnetic fields. These fields interact with the motor's rotor, which contains permanent magnets, causing it to step. The meticulous design and engineering behind these motors ensure they deliver precise movements every single time, making them invaluable in applications where accuracy is paramount.
Nema 23 stepper motors encapsulate a perfect synergy of design, power, and precision, making them a cornerstone in numerous applications that rely on controlled movement. Whether you're an artist working on a CNC masterpiece, an engineer prototyping a new device, or a hobbyist delving into the world of robotics, the Nema 23 is a reliable companion on your journey.
Key Specifications:
The vast realm of CNC machining, robotics, and automation relies heavily on components being standardized. This ensures compatibility, replaceability, and a general understanding across industries. With the Nema 23 stepper motor being one of the most widely used stepper motors, understanding its key specifications becomes imperative for enthusiasts and professionals alike. Here's a more detailed look:
- Torque: This is often the first specification that users consider. Torque defines the rotational force the motor can exert. In essence, it tells us how much 'strength' the motor has. For Nema 23 motors, torque can range from as low as 0.5 Nm for less demanding applications to as high as 2.2 Nm (or even more in some specialized variants) for more heavy-duty tasks. It's crucial to choose a motor with the right torque for your application to ensure efficiency and prevent motor strain.
- Steps per Revolution: Stepper motors move in steps. The number of steps taken to complete a full 360° rotation defines its resolution. Commonly, a standard Nema 23 motor will offer 200 steps per revolution, resulting in a 1.8° step angle. However, there are variants with higher resolutions, achieved using techniques like micro-stepping, which subdivides these steps further.
- Voltage and Current Ratings: These parameters determine the electrical power the motor requires for optimal operation. Overloading the motor with higher voltage or current than it's rated for can lead to overheating and damage. Conversely, underpowering will yield sub-optimal performance. Often, the voltage isn't directly specified; instead, the resistance and rated current are given, which can be used to calculate the appropriate voltage using Ohm's Law.
- Inductance and Resistance: The winding inductance and resistance of a stepper motor play a crucial role in its performance. While inductance determines how quickly current builds up in the windings, resistance affects the motor's heat generation and efficiency. A motor with lower inductance can typically be driven at higher speeds but might require a more capable driver.
- Shaft Size and Type: The motor's shaft is where the rotary motion gets transferred to the machine or tool. Nema 23 motors usually come with a standard shaft diameter, but lengths can vary. Additionally, shafts can be single, double-ended, or even feature a keyway or flat section to prevent slippage when coupled with gears or pulleys.
- Physical Dimensions: While the face size is standardized at approximately 2.3 inches (58.4 mm), the motor's length can vary. Longer motors typically indicate more winding or more powerful magnets, which can result in higher torque. Ensuring the motor fits within your setup's spatial constraints is vital.
- Thermal Specifications: Motors produce heat when in operation, especially under heavy loads. Each motor will have a specified maximum operating temperature. To ensure longevity, it's essential that the motor doesn't consistently operate close to or beyond this limit. Adequate ventilation, cooling solutions, or heat sinks can be employed to manage heat.
When you're faced with a datasheet for a Nema 23 stepper motor, understanding these specifications can greatly influence the success and efficiency of your project. It's like knowing the ingredients before cooking a dish; the more familiar you are with them, the better the outcome.
Practical Applications:
Nema 23 stepper motors, with their blend of size, torque, and precision, find utility in a wide range of applications. Their adaptability, combined with the consistency they provide, has made them popular choices in both commercial industries and DIY communities. Here's an expanded look at where these motors shine:
CNC Machines:
- Milling Machines: Precision is paramount when milling. Whether you're working with wood, metal, or any other material, the motor's ability to move in exact increments ensures that the cuts are accurate.
- Lathes: For turning operations, the motor’s consistent rotation, combined with its torque, allows for smooth cuts along the entirety of a workpiece.
- Laser Cutters and Engravers: Precision movement is key when engraving intricate patterns or cutting out detailed shapes, especially on materials that are sensitive to overexposure.
- Plasma Cutters: Here, the motor's ability to move without hesitation or jitter is crucial, ensuring clean cuts through metals.
3D Printers:
- While smaller printers often use Nema 17 motors, larger format 3D printers or those designed for specialized materials may use Nema 23 motors for the added stability and force, especially on the X and Y axes where bed size increases inertia.
- In dual-extrusion printers or those with heavy hotends, the added torque can prevent skipping steps during rapid movements.
Robotics:
- Robotic Arms: Especially in pick-and-place machines or assembly line robots, the consistent, controlled movement of Nema 23 motors ensures objects are moved accurately.
- Mobile Robots: For robots navigating terrains or carrying weight, the added torque from a Nema 23 can be beneficial.
- Automated Guided Vehicles (AGVs): Used in warehouses and large factories, the Nema 23 motors can provide the torque needed to move goods while maintaining precision in navigation.
Linear Motion Systems:
- In applications where linear (straight-line) movement is needed, such as automated sliding doors, conveyor systems, or camera sliders, the rotary motion of Nema 23 motors can be converted to linear motion using mechanisms like lead screws or belts and pulleys.
Medical Equipment:
- Precision instruments like automated pipetting systems, sample analyzers, or specialized scanning devices rely on the consistency and reliability of stepper motors to handle sensitive and precise tasks.
Art Installations and Theatrical Equipment:
- Automated art installations might require intricate and precise movements, which the Nema 23 can deliver. Similarly, in theatre, for moving props or creating special effects, these motors provide reliable and repeatable movements.
Telescopes:
- For astrophotography or star tracking, the precise movements of a Nema 23 motor can be crucial. These motors can slowly and accurately move a telescope to track celestial bodies, ensuring clear, streak-free images over long exposure times.
The Nema 23 stepper motor's range of practical applications is a testament to its versatility and reliability. Its design, which emphasizes precision and torque, allows it to be a workhorse in many industries and projects. Whether you're building a large-scale industrial system or a DIY project at home, there's a good chance that the Nema 23 can play a pivotal role in bringing your vision to life.
Setting Up Nema 23 for Your Project:
Implementing the Nema 23 stepper motor into your project is not just about plugging it in and hoping for the best. Proper setup is essential to harness its full potential, ensure longevity, and avoid any unforeseen issues. Below is a comprehensive guide to help you integrate the Nema 23 seamlessly:
Choosing the Right Driver:
- The driver is the bridge between your motor and the control system. It dictates the power and control signals sent to the motor.
- Ensure your driver is compatible with the motor's voltage, current, and microstepping specifications.
- For optimal performance, choose a driver that has protection features, like overcurrent protection or thermal shutdown.
Wiring and Connections:
- Motor Phases: Nema 23 motors typically come with four wires, corresponding to two motor phases. However, some variants may have six or eight wires for additional configuration flexibility.
- Color Coding: While there's a general standard for wire colors, always refer to the specific datasheet of your motor, as colors can vary between manufacturers.
- Secure Connections: Use proper connectors, ensure tight connections, and consider using ferrules or soldering for added reliability.
- Cable Management: Use cable chains or conduits to avoid wire tangling, which can cause wear or disconnections during movement.
Powering the Motor:
- Based on the motor's voltage and current ratings, choose a power supply that can meet or exceed these requirements.
- Ensure that the power supply has a bit of overhead, typically 20-30% more than what the motor might draw, to cater to potential spikes or increased loads.
- Implementing a fuse between the power supply and the driver can add a layer of protection against overcurrent situations.
Configuring the Driver:
- Microstepping: Many modern drivers offer microstepping, which divides the motor's basic step angle into smaller increments, providing smoother motion. Choose the appropriate setting based on your need for precision versus speed.
- Current Limiting: To prevent overheating, set the driver to limit the current to the motor's rated maximum or slightly below.
- Acceleration/Deceleration: Setting a gradual acceleration and deceleration can prevent sudden jerks, reducing mechanical stress and improving accuracy.
Mechanical Setup:
- Mounting: Ensure the motor is securely fastened to prevent vibrations. Use appropriate brackets or mounts designed for Nema 23 motors.
- Couplings: If connecting the motor to a lead screw or another mechanical system, use flexible couplings. This can compensate for any minor misalignments and reduce stress on the motor's bearings.
- Alignment: Ensure that any connected mechanical systems are properly aligned. Misalignment can cause increased wear and reduce the motor's efficiency and life.
Test Runs:
- Before fully integrating the motor into your system, perform test runs. Start at low speeds and power, gradually ramping up to ensure everything operates smoothly.
- Monitor the motor's temperature during these tests. If the motor becomes too hot to touch, it may be drawing too much current or facing mechanical resistance.
Feedback Systems (Optional):
- While stepper motors inherently move to predefined positions, for applications where extreme precision is required, consider integrating feedback systems like encoders. This can compensate for any missed steps and provide real-time position feedback.
Setting up the Nema 23 motor properly is an investment in the longevity and efficiency of both the motor and your project. By following the guidelines and always referring to the specific datasheets and manuals provided by the manufacturer, you'll be on your way to harnessing the full power and precision of the Nema 23.
Tips for Maximum Efficiency:
Efficiency in the realm of stepper motors is about achieving desired motion outcomes with minimum energy consumption and wear. Here's a guide on how to extract the most from your Nema 23 motor while ensuring it operates at peak efficiency:
- Optimized Power Supply: Use a power supply that matches the motor's voltage and current requirements. Avoid using one that's drastically overpowered, as it may lead to unnecessary energy wastage or overheating.
- Cooling Systems:
Active Cooling: Using a fan or dedicated cooling system can help dissipate heat more effectively, especially during prolonged operations.
Passive Cooling: Implementing heat sinks on the motor or driver can passively draw away heat, improving efficiency. - Tune Your Driver Settings:
Dynamic Current Control: Some drivers allow for dynamic current control, adjusting current based on the motor’s load. This ensures that the motor uses only as much power as needed.
Adjust Decay Mode: Modern drivers often provide adjustable decay modes, influencing how the motor handles power during non-active phases. Tuning this can help in reducing heat and improving efficiency. - Regular Maintenance:
Cleaning: Dust and debris can impede heat dissipation. Regularly clean the motor and its surroundings.
Lubrication: If your setup involves lead screws or gears, ensure they're well-lubricated to reduce friction and enhance motor efficiency. - Minimize Mechanical Resistance: Ensure all moving parts connected to the motor are free of obstructions and run smoothly. The more resistance the motor faces, the harder it has to work, reducing its efficiency.
- Optimal Acceleration/Deceleration Curves: Sudden starts or stops can be energy-intensive and wear down components faster. Setting up smoother acceleration and deceleration curves in your driver can lead to more efficient motor operations.
- Reduce Idle Times: When not in use, especially for extended periods, consider powering down the motor or putting it in a low-power standby mode. This reduces unnecessary heat generation and power consumption.
- Feedback Systems: Although one of the stepper motor's perks is its open-loop control, integrating feedback systems like encoders can help in applications where maximum efficiency is crucial. It allows for real-time adjustments, ensuring the motor operates optimally.
- Optimized Step Rates: There’s often an optimal speed range where the motor runs most efficiently. Running too slow can be as inefficient as running too fast. Find that sweet spot, typically provided in torque-speed curves in the motor's datasheet.
Microstepping for Smoothness: Microstepping not only provides smoother motion but can also reduce mechanical vibrations and stresses. This can lead to less wear and energy wastage in the long run. - Cable and Connector Quality: High-quality cables and connectors ensure minimal energy is lost during transmission. It’s a small detail, but in setups where every ounce of efficiency counts, it matters.
- Regular Calibration: Over time, components can drift out of calibration. Regularly calibrate your system to ensure that the motor doesn't overwork due to misalignments or inconsistencies.
Harnessing the maximum efficiency of your Nema 23 motor is a blend of using quality components, regular maintenance, and understanding the motor's operational sweet spots. It not only leads to energy savings but also ensures a longer and more productive life for your motor. With these tips in hand, you're well on your way to an optimized and efficient motion solution.
Wrapping Up
The Nema 23 stepper motor, like many mechanical and electrical components, represents a fusion of innovation, engineering, and design that serves various industries and hobbyist projects. Its prominence in diverse fields such as CNC machining, robotics, and medical equipment is a testament to its versatility and robustness. With an optimal balance of size, torque, and precision, it provides a middle ground that caters to both small-scale detailed tasks and larger, more power-demanding applications.
Yet, as with any tool or component, extracting its full potential and ensuring longevity requires understanding, careful setup, and routine maintenance. The sheer adaptability of the Nema 23 means that it’s more than just a motor—it's a promise of consistent and reliable motion when integrated correctly. As technology advances and applications grow even more complex, the foundational principles of this stepper motor remind us of the importance of precision, power, and adaptability. Whether you’re a seasoned engineer or an enthusiastic DIYer, understanding the intricacies of the Nema 23 equips you with a powerful tool in the world of motion and automation.
Remember, as with all tools and components, the key is understanding, respect, and care. Happy Machining! 🛠️