From Rough Cut to Fine Detail: Essential Bits and End Mills for Wood
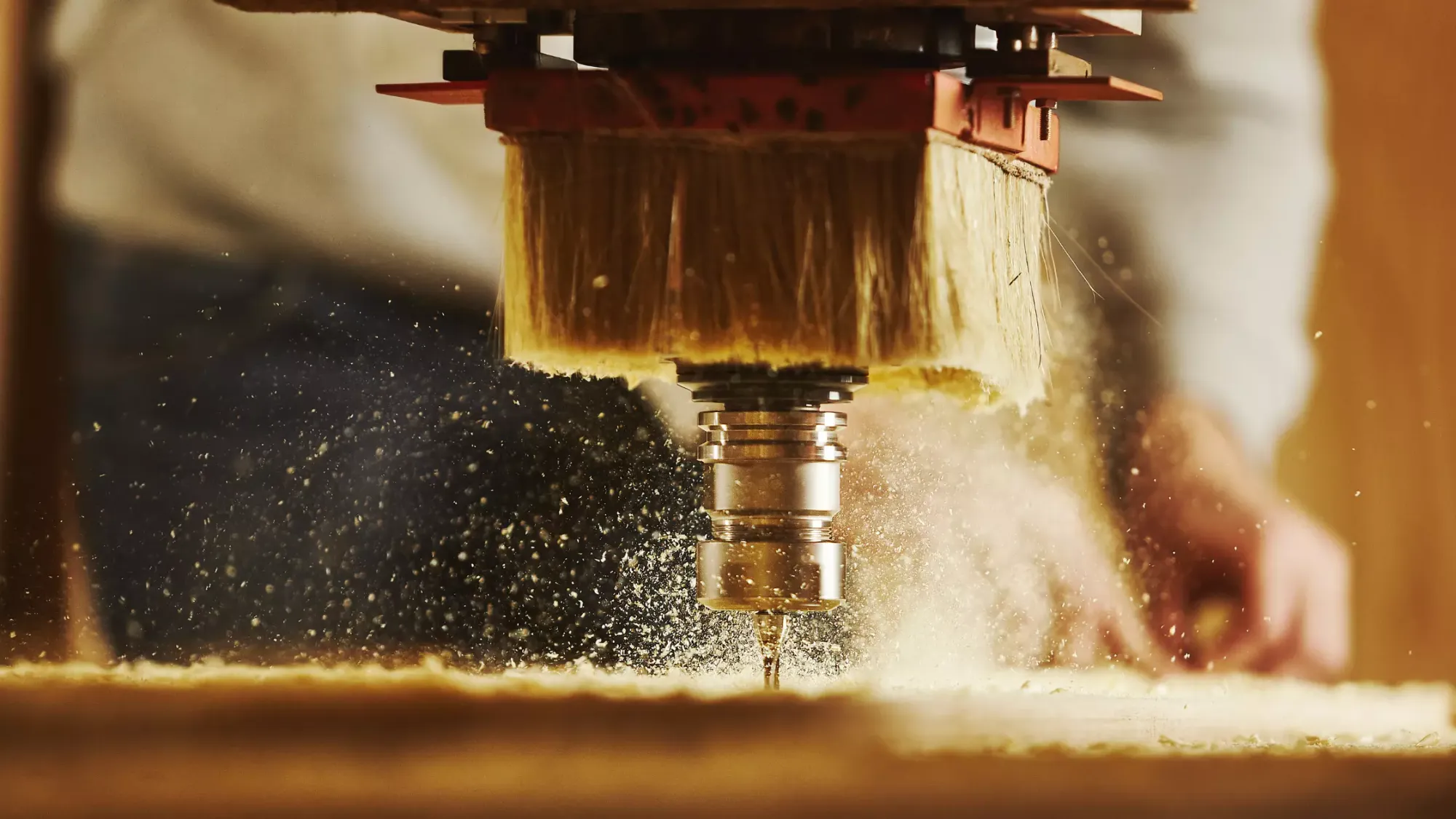
In the world of CNC machining, the tools you choose can make or break your project. Especially when it comes to wood, selecting the right endmill or bit is crucial for achieving that perfect finish and precise cut. The intricacies of wood as a material demand tools that are tailored to handle its unique properties, from the hardness of oak to the softness of pine. Each wood type presents its challenges, and having the right tool can be the difference between a masterpiece and a piece of scrap.
For both hobbyists and professionals alike, understanding the nuances of these tools can elevate the quality of your work, ensuring that each piece stands out. With the vast array of options available in the market, it's easy to get overwhelmed. This guide aims to simplify that choice, highlighting the essential end mills and bits specifically designed for wood machining, helping you navigate the complexities of CNC woodworking with confidence.
Understanding End Mills and Bits
Before we dive into specifics, it's essential to understand the difference between an endmill and a bit. While both are cutting tools used in CNC machines, end mills are typically used in milling applications, whereas bits are often associated with routers. However, the terms are sometimes used interchangeably in the woodworking community, leading to some confusion among beginners.
- End Mills: End mills are multi-functional tools used primarily in milling operations. They come in various shapes and sizes, each designed for specific tasks. The flutes, which are the deep helical grooves running up the cutter, play a crucial role in chip evacuation. More flutes mean a smoother cut, but they may struggle with chip evacuation, especially in deeper cuts. Fewer flutes allow for faster chip evacuation but might result in a rougher finish. The material of the end mill, such as carbide or high-speed steel, also affects its performance and longevity.
- Bits: Bits, on the other hand, are predominantly used with routers. They are designed to hollow out an area in a piece of wood or create intricate patterns. Router bits come in a plethora of shapes, from straight-cutting bits to more specialized forms like dovetail or chamfer bits. The sharpness and geometry of the bit's cutting edge determine the quality of the finish. For instance, spiral router bits, with their twisted design, help in achieving a smoother finish by reducing the risk of "tear-out" in the wood.
- Material Considerations: Both end mills and bits come in various materials, with carbide being one of the most popular due to its hardness and heat resistance. However, the choice of tool material should align with the type of wood being machined. Softer woods might not require the hardness of a carbide tool, whereas hardwoods, which are more abrasive, benefit from the durability of carbide.
While end mills and bits serve similar purposes in cutting and shaping wood, their design, application, and optimal use cases differ. By understanding these nuances, woodworkers and CNC enthusiasts can make informed decisions, ensuring the longevity of their tools and the quality of their projects.
1. Upcut End Mills
Upcut end mills are a popular choice in the CNC machining world, especially when it comes to woodworking. Their primary characteristic is the upward direction of their spiral flutes, which gives them their name. This design ensures that as the tool rotates and moves through the material, the wood chips are pulled up and out of the cut.
Design and Functionality
The spiral design of upcut end mills is intentional and serves a specific purpose. As the end mill rotates, the spiral flutes create a pulling action, effectively lifting the wood chips away from the workpiece. This design ensures efficient chip removal, which is particularly beneficial for deep cuts or when working with materials that generate a lot of debris. Efficient chip removal not only ensures a cleaner cut but also reduces the risk of chip re-cutting, which can degrade the quality of the finish.
Benefits
- Efficient Chip Evacuation: The primary advantage of upcut end mills is their ability to clear away waste material effectively. This is crucial for preventing chip congestion in the cutting area, which can lead to tool breakage or burning of the material.
- Cooler Operation: Because the chips are swiftly removed from the cutting area, there's less friction and heat buildup. This results in a cooler operation, prolonging tool life and preserving the integrity of the workpiece.
- Deep Cutting Capability: For operations that require deep grooves or pockets, upcut end mills are the go-to choice due to their superior chip evacuation capabilities.
Considerations
While upcut end mills offer several advantages, they do have a few drawbacks. The upward pulling action can cause fraying or splintering on the top surface of the workpiece. This is especially noticeable in laminated materials or plywood, where the top layer can get lifted. Therefore, while they're excellent for efficient chip removal, they might not always provide the cleanest finish on the top surface.
Applications
Upcut end mills are versatile and can be used for a variety of applications, including:
- Slotting and pocketing
- Deep cavity milling
- Roughing operations where finish is not a primary concern
Upcut end mills are an invaluable tool in the arsenal of a CNC machinist, especially for tasks that require efficient chip removal. However, like all tools, understanding their strengths and limitations is key. By choosing the right tool for the job and considering the material being machined, one can achieve optimal results with upcut end mills.
2. Downcut End Mills
Downcut end mills, often referred to as "down spiral" end mills, are distinguished by the downward orientation of their spiral flutes. As the name suggests, these end mills push chips downward as they cut, making them particularly suitable for certain woodworking applications where surface finish is paramount.
Design and Functionality
The spiral flutes of downcut end mills are designed to push the wood fibers down as the tool moves through the material. This downward pressure ensures that the top surface of the workpiece remains clean and free from fraying or splintering, especially at the entry point of the cut.
Benefits
- Superior Top Surface Finish: The primary advantage of downcut end mills is their ability to produce a clean, smooth finish on the top surface of the workpiece. This is especially beneficial when working with veneered or laminated materials where preserving the surface finish is crucial.
- Reduced Fraying: Downcut end mills are excellent for reducing fraying or splintering, especially on the edges of the workpiece. This makes them ideal for tasks like dado cuts or inlay work.
- Less Material Lifting: The downward pressure exerted by the tool helps in holding the material firmly against the worktable or CNC bed, reducing the chances of material lifting or shifting during machining.
Considerations
While downcut end mills offer a superior finish on the top surface, they come with their set of challenges. The most notable is chip evacuation. Since the chips are pushed downward, there's a risk of them getting trapped or compacted in the cut, especially in deeper pockets or grooves. This can lead to increased heat, tool wear, and even burning of the material. It's essential to account for this by adjusting feed rates, using appropriate tool paths, or combining operations with other end mill types.
Applications
Downcut end mills are versatile and find applications in various woodworking tasks, including:
- Edge routing for a splinter-free finish
- Creating inlays or recessed logos
- Pocketing operations where the top surface finish is critical
- Cutting out parts with a clean top edge
Downcut end mills are a valuable tool for woodworkers and CNC enthusiasts, especially when a pristine top surface finish is the goal. By understanding their strengths and potential challenges, users can harness their capabilities effectively. As with all tools, the key lies in choosing the right end mill for the specific task at hand and using it in conjunction with other tools and techniques to achieve the best results.
3. Compression End Mills
Compression end mills, sometimes referred to as "compression cutters," combine the best of both upcut and downcut end mills. They are designed with spiral flutes that start as upcut at the tip and transition to downcut along the length. This unique design allows them to push chips both upward and downward, making them especially suitable for cutting layered materials like plywood or laminated panels.
Design and Functionality
The genius behind the compression end mill lies in its dual-directional flutes. The bottom part of the cutter, where the upcut flutes are located, pulls chips upward, while the upper part, with its downcut flutes, pushes chips downward. This ensures that both the top and bottom surfaces of the workpiece are cleanly cut, minimizing splintering or fraying on either side.
Benefits
- Clean Finish on Both Surfaces: Compression end mills excel in providing a smooth finish on both the top and bottom surfaces of the material. This is particularly beneficial when cutting through materials where both sides will be visible in the final product.
- Reduced Splintering: The dual-directional design ensures that the edges of the material, especially materials like plywood or MDF, remain splinter-free.
- Efficient Chip Evacuation: While the upcut portion helps in lifting the material, the downcut part assists in chip evacuation, reducing the risk of chip re-cutting and heat buildup.
- Stable Material Hold-Down: The compression action helps in holding the material firmly against the CNC bed, reducing the chances of material lifting or warping during the cutting process.
Considerations
While compression end mills offer many advantages, they require careful consideration regarding feed rates and cutting depths. It's crucial to ensure that the transition point between the upcut and downcut flutes aligns correctly with the surface of the material to maximize the tool's benefits. Additionally, they might be more expensive than single-direction end mills, but the quality of finish often justifies the cost.
Applications
Compression end mills are versatile and are particularly favored in applications such as:
- Cutting double-sided laminates or veneered materials
- Producing parts where both top and bottom finishes are critical
- Slotting and pocketing tasks in layered materials
- Sign-making and furniture production where edge finish is paramount
Compression end mills stand out as a unique and invaluable tool in the CNC machining world, especially for tasks demanding a high-quality finish on both sides of the material. By understanding their design and optimizing their use, woodworkers and machinists can achieve unparalleled results, making these end mills a worthy addition to any tool collection.
4. Ball Nose Bits
Ball nose bits, often referred to as "ball nose end mills," are a type of milling cutter characterized by their hemispherical tip. They are primarily used in CNC machining and milling operations to produce a smooth, contoured surface, making them especially popular in intricate carving, sculpting, and 3D modeling tasks.
Design and Functionality
The defining feature of a ball nose bit is its rounded tip, which contrasts with the flat tip of a standard end mill. This spherical design allows the tool to create curved surfaces with ease. As the tool moves through the material, the rounded tip ensures that the cut's depth gradually changes, resulting in a smooth, scallop-free finish.
Benefits
- Smooth Contoured Surfaces: Ball nose bits excel in producing a seamless, contoured finish, making them ideal for sculpting and intricate carving tasks.
- Versatility: They can be used for both roughing and finishing operations. While they can remove material quickly, they can also be used for detailed finishing touches.
- Reduced Tool Marks: The rounded design ensures minimal tool marks, resulting in a smoother surface that often requires less post-processing.
- 3D Profiling: Ball nose bits are the go-to choice for 3D profiling tasks, where the objective is to replicate a 3D model in a physical material.
Considerations
While ball nose bits offer a smooth finish, they come with a few challenges. Due to their rounded tip, they might not be as efficient in removing large amounts of material as flat end mills. The depth of cut is also crucial; too shallow, and you might end up with scalloping. The tool's diameter, combined with the depth of cut, will determine the surface finish, so it's essential to choose the right size for the job.
Applications
Ball nose bits find applications in a wide range of tasks, including:
- Detailed 3D carving and sculpting
- Mold and die making, where a smooth surface is crucial
- Engraving tasks that require a rounded bottom groove
- Creating channels or grooves with a rounded bottom
- Artistic woodworking projects, such as relief carvings or intricate inlays
Ball nose bits are a staple in the CNC machining world, especially when the task demands a smooth, contoured finish. Their unique design allows for precision and finesse, making them indispensable for detailed and artistic projects. By understanding their strengths and potential challenges, users can harness their capabilities to produce stunning results that stand out in both form and function.
5. V-bits
V-bits, commonly known as "V-carve bits" or "engraving bits," are distinguished by their V-shaped tip. They are a favorite in the CNC routing and engraving world, particularly for tasks that require fine detailing, sharp corners, or intricate designs. Their unique geometry allows for varying cut depths depending on the width of the cut, making them ideal for detailed work.
Design and Functionality
The hallmark of a V-bit is its angular, conical design. The angle of the V can vary, with common angles being 30°, 45°, 60°, and 90°. The chosen angle determines the width and depth of the cut. As the bit is plunged deeper into the material, the cut becomes wider, allowing for variable-width channels with a single tool. This makes V-bits incredibly versatile, especially for tasks like lettering or decorative engraving.
Benefits
- Precision Detailing: V-bits are perfect for tasks that demand fine lines and sharp corners, such as intricate designs or lettering.
- Variable Cut Depths: The conical shape allows for cuts of varying widths and depths with the same tool, depending on how deep the bit is plunged into the material.
- Clean, Sharp Corners: The pointed tip ensures that corners are sharp and well-defined, which is especially beneficial for tasks like logo engraving or detailed inlays.
- Efficient Material Removal: For engraving tasks, V-bits can remove material efficiently, providing both depth and precision.
Considerations
While V-bits are exceptional for detailed work, they have limitations. Their pointed tip is delicate and can break under excessive force or if used improperly. They're also not ideal for large material removal tasks, as their design prioritizes precision over bulk cutting. The choice of V-bit angle is crucial; a steeper angle (like 30°) is better for fine lines, while a shallower angle (like 90°) is suited for broader cuts.
Applications
V-bits are versatile and find applications in various tasks, including:
- Detailed engraving on materials like wood, metal, or acrylic
- Sign-making, especially for lettering or logos
- Creating decorative inlays with sharp corners
- PCB (printed circuit board) engraving for tracing fine lines
- Artistic woodworking projects that require intricate detailing
V-bits are an invaluable tool for anyone looking to achieve precision and detail in their CNC projects. Their unique design allows for a level of finesse that few other bits can match. By understanding their strengths, potential challenges, and optimal use cases, craftsmen can leverage V-bits to elevate the quality and intricacy of their work, producing results that truly stand out.
Summing Up
Choosing the right endmill or bit for your wood machining project is essential for achieving the desired results. By understanding the unique characteristics and applications of each tool, you can ensure a smooth, clean cut every time. The world of CNC woodworking is vast, and the tools you select play a pivotal role in determining the outcome of your projects. Whether you're crafting a delicate piece of art or constructing robust furniture, the endmill or bit you choose can significantly influence the quality, precision, and finish of your work.
Beyond just the technical aspects, there's an art to CNC woodworking. The tools you select play a significant role in bringing your vision to life, allowing you to craft pieces that resonate with both functionality and aesthetic appeal. As you delve deeper into the realm of CNC machining, remember that it's not just about the machine or the material. It's about the harmony between your tools, your creative intent, and the wood you're working with. Embrace the journey, and let your tools be the trusted companions that help you create woodworking magic.