Endmill Speeds: Getting it Right
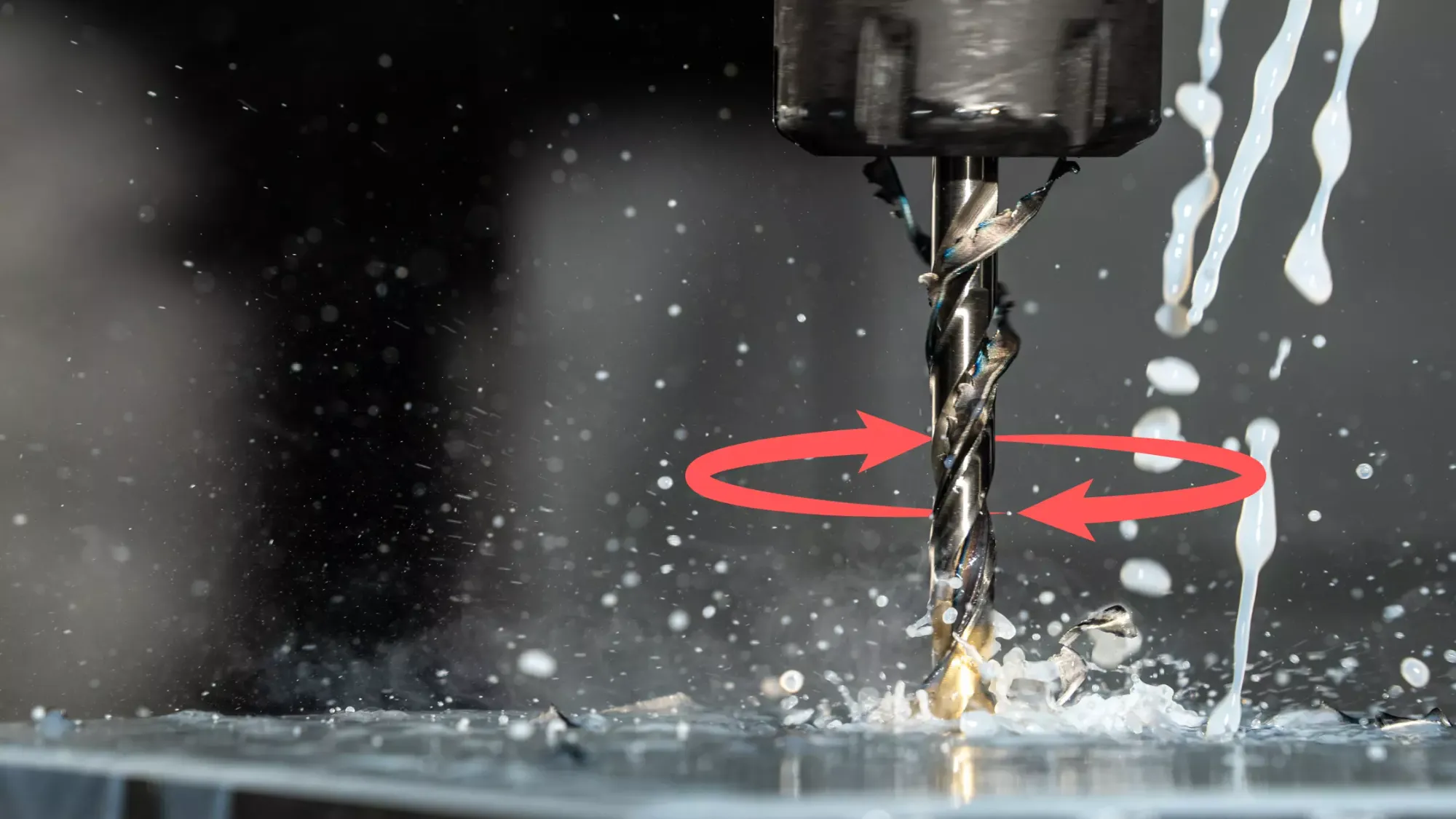
In the intricate realm of CNC machining, the endmill stands out as one of the most pivotal tools in a machinist's arsenal. Its performance, largely determined by its speed setting, can significantly influence the precision, finish, and overall quality of your final product. However, with the myriad of materials and endmill types available, determining the optimal speed can seem like a daunting task.
Yet, fear not! With a solid understanding of the basics and a few practical tips, you can master the art of endmill speed setting. Whether you're a seasoned machinist or just starting out, this guide aims to provide you with the essential knowledge and confidence to ensure that your CNC projects always meet the highest standards of excellence.
Understanding Surface Speed
Surface speed, often denoted as surface feet per minute (SFM), is a foundational concept in CNC machining. It represents the speed at which the endmill's cutting edge moves through the material being machined. Different materials have varying SFM values, primarily because each material has its own unique properties that affect how it interacts with the cutting tool. For instance, aluminum, being a softer metal, might have an SFM of 250-300, while a harder metal like steel might be around 100-150.
But why is SFM so crucial? The surface speed directly impacts the heat generated during the cutting process. Too high an SFM can cause excessive heat, leading to premature tool wear and potential damage to the workpiece. On the other hand, an SFM that's too low can result in inefficient cutting and longer machining times.
To determine the optimal SFM for a particular material, it's always a good idea to refer to the manufacturer's guidelines or industry-standard charts. These resources provide recommended SFM values based on extensive testing and real-world experience. However, it's also essential to factor in the specific conditions of your machining setup, such as the rigidity of your machine and the type of coolant used, as these can influence the ideal SFM.
Understanding and correctly setting the surface speed is a delicate balance that ensures efficient cutting, prolongs tool life, and produces a high-quality finish on the workpiece.
The Role of Diameter
The diameter of the endmill is a fundamental parameter that directly influences the rotational speed (RPM) of the tool during machining. It's a simple yet profound relationship: as the diameter of the endmill increases, the circumference (or the distance the cutting edge travels in one rotation) also increases. This means that for a larger-diameter endmill to achieve the same surface speed (SFM) as a smaller one, it must rotate at a slower RPM.
Let's delve into the mathematics a bit. The formula to determine the RPM based on the desired SFM and the diameter of the endmill is:
RPM = (SFM × 3.82) / Diameter
This equation showcases the inverse relationship between diameter and RPM. For instance, if you were to double the diameter of the endmill while keeping the SFM constant, the RPM would need to be halved to maintain the same cutting conditions.
Beyond the math, the diameter also plays a pivotal role in other machining aspects:
- Tool Strength and Rigidity: Larger diameter endmills tend to be more rigid and can resist deflection better than their thinner counterparts. This rigidity allows them to handle higher cutting forces, making them suitable for roughing operations.
- Surface Finish: Smaller diameter endmills, due to their higher RPM capabilities at the same SFM, can produce smoother surface finishes. They are often preferred for finishing operations where precision and aesthetics are paramount.
- Reach and Accessibility: While larger diameter tools offer strength, smaller diameters provide better reach and accessibility, especially in intricate or tight geometries. This makes them invaluable for detailed or complex parts.
- Heat Dissipation: A larger diameter endmill has a more significant contact area with the material, which can lead to increased heat generation. Proper cooling and lubrication become even more critical in such cases to prevent tool wear and material damage.
The diameter of the endmill is not just a dimension; it's a key determinant of the tool's performance, capabilities, and the results it can achieve. Selecting the right diameter for a specific task, while also considering its speed implications, is crucial for successful CNC machining.
The Importance of Flutes
Flutes are the grooves or valleys cut into the body of the endmill, and they play a multifaceted role in the machining process. Their primary function is to provide a path for chip evacuation while also engaging the workpiece to produce a cut. The number, design, and geometry of these flutes can significantly influence the performance and outcome of a machining operation.
- Chip Evacuation: One of the primary roles of flutes is to facilitate the removal of chips from the cutting area. Efficient chip evacuation is crucial to prevent recutting of chips, which can lead to increased heat, tool wear, and potential damage to the workpiece.
- Feed Rate and Chip Load: The number of flutes directly affects the chip load, which is the amount of material removed by each cutting edge during a single rotation. More flutes mean a reduced chip load per tooth, leading to a smoother finish. However, this also means that the feed rate might need to be adjusted to prevent overloading the tool.
- Surface Finish: Endmills with a higher number of flutes tend to produce a finer surface finish. This is because the increased number of cutting edges results in more frequent cuts, reducing the scallop height on the finished surface.
- Tool Strength and Rigidity: Endmills with fewer flutes generally have deeper gullet spaces, allowing for better chip evacuation in materials that produce larger chips, like aluminum. However, this design can reduce the tool's core strength. Conversely, tools with more flutes have a more substantial core, making them more rigid and suitable for harder materials.
- Heat Generation and Dissipation: More flutes can lead to increased heat generation due to the higher frequency of cuts. Proper cooling and lubrication become essential, especially when using endmills with a higher number of flutes, to prevent excessive heat buildup.
- Material Compatibility: The number of flutes is often chosen based on the material being machined. For instance, softer materials like aluminum benefit from endmills with fewer flutes (2 or 3) because they produce larger chips that need ample space for evacuation. Harder materials like stainless steel, on the other hand, are often machined with tools that have 4 or more flutes, as these materials produce smaller chips and benefit from the increased rigidity of the tool.
- Tool Life: Properly matching the number of flutes to the material and application can extend tool life. An endmill with an inappropriate number of flutes for a particular task may wear out faster due to inefficient chip evacuation, excessive heat, or undue stress on the tool.
Flutes are not just a design feature of endmills; they are a critical component that determines how the tool interacts with the material, the quality of the finish, and the overall efficiency of the machining process. Understanding their importance and selecting the right endmill based on the number of flutes is essential for achieving optimal machining results.
Material Matters
The material being worked on is not just a passive recipient of the cutting action; it actively influences the entire machining process. The type of material dictates a range of factors, from the choice of endmill to the appropriate speed and feed settings. Understanding the nuances of different materials is paramount for achieving precision, efficiency, and longevity in machining operations.
- Material Hardness: The hardness of a material, often measured on the Rockwell or Brinell scale, directly impacts the cutting speed and tool choice. Harder materials resist cutting forces more than softer ones, necessitating slower speeds and more robust, often carbide, tooling.
- Thermal Conductivity: Materials like aluminum, which have high thermal conductivity, dissipate heat quickly. This characteristic allows for faster machining speeds without the risk of excessive heat buildup. Conversely, materials with low thermal conductivity, like titanium, retain heat at the cutting zone, requiring careful speed, feed, and coolant considerations.
- Material Toughness: Tough materials tend to be more resistant to chipping and breaking but can cause rapid tool wear due to the continuous and high cutting forces involved. Adjusting feed rates and ensuring sharp tooling can mitigate these challenges.
- Chemical Reactivity: Some materials, like certain stainless steels, can chemically react with the cutting tool under high temperatures, leading to tool degradation. In such cases, using coated tools and proper coolants can help reduce this adverse effect.
- Work Hardening Potential: Materials like austenitic stainless steel have a tendency to harden rapidly when subjected to machining operations. If not accounted for, work hardening can lead to premature tool wear and poor surface finish. Continuous, aggressive cuts with adequate feed rates can help avoid work hardening.
- Material Grain Structure: The grain structure, whether fine or coarse, can influence the finish quality. Materials with a fine grain structure tend to provide smoother finishes, while those with a coarse grain structure might result in a rougher surface.
- Elasticity and Plasticity: Elastic materials tend to spring back slightly after being cut, which can affect dimensional accuracy. Plastic materials, on the other hand, can deform permanently under the cutting force. Understanding these properties is crucial for achieving tight tolerances.
- Chip Formation: Different materials produce chips of varying shapes and sizes. Efficient chip evacuation is vital to prevent recutting and tool clogging. The material's chip formation tendency can influence the choice of flute design and number.
- Material Cost and Availability: Beyond the machining characteristics, the cost and availability of materials can influence production decisions. Rare or expensive materials might necessitate more conservative machining parameters to minimize wastage.
The material is not just a backdrop for machining; it's an active participant that dictates a host of decisions. A deep understanding of the material's properties, behaviors, and quirks is essential for any machinist aiming for excellence. By respecting the material and adapting to its unique demands, one can achieve optimal machining outcomes every time.
Machine Limitations
Understanding the limitations of the machines used is as crucial as knowing their capabilities. While these machines are marvels of modern engineering, designed to achieve high precision and repeatability, they are not without their constraints. Recognizing and respecting these limitations ensures not only the safety and longevity of the equipment but also the quality and efficiency of the machining process.
- Speed and Feed Limits: Every CNC machine has maximum and minimum speed and feed rates. Pushing the machine beyond these rates can result in tool breakage, machine wear, or even catastrophic failure.
- Axis Movement Restrictions: Depending on the design, a CNC machine might be limited in its axis movements. For instance, a 3-axis machine won't have the rotational capabilities of a 5-axis machine, limiting the complexity of parts it can produce.
- Work Envelope Constraints: The work envelope defines the maximum size of the part that can be machined. Exceeding this space can lead to collisions or incomplete machining.
- Tooling Limitations: Machines are designed to handle specific tool sizes and types. Using inappropriate tooling can lead to suboptimal results or damage.
- Material Compatibility: Not all CNC machines are equipped to handle all materials. For example, a machine designed for wood might struggle with harder metals, leading to rapid tool wear or poor finishes.
- Coolant and Lubrication Systems: The effectiveness of a machine's coolant and lubrication system can limit the materials and speeds at which it can operate efficiently.
- Vibration and Stability: All machines have inherent vibration frequencies. Operating at these frequencies can lead to resonance, affecting the quality of the cut and potentially damaging the machine.
- Software Constraints: The machine's controller and software might have limitations in terms of the complexity of the programs it can run, the file sizes it can handle, or the precision of the movements.
- Thermal Expansion: Machines are subject to thermal expansion, which can affect precision. Continuous operation or lack of proper cooling can lead to deviations in part dimensions.
- Maintenance and Wear: Over time, components wear out, and the machine's accuracy can degrade. Regular maintenance is essential, but even with the best care, machines have a finite lifespan.
A seasoned machinist understands these limitations and works within them, leveraging the machine's strengths while mitigating its weaknesses. By doing so, they ensure that the machine serves as a reliable partner in the intricate ballet of material transformation, producing parts that meet the highest standards of precision and quality.
Experimentation is Key
While theoretical knowledge, guidelines, and manufacturer recommendations provide a solid foundation, there's no substitute for hands-on experimentation. Every machining setup is unique, encompassing a blend of tools, materials, machines, and environmental factors. This dynamic nature means that what works best in one scenario might not be optimal in another. Here's why embracing a spirit of experimentation is indispensable for machinists:
- Discovering Sweet Spots: While charts and guidelines offer general speed and feed recommendations, each machine has its own "sweet spot" where it operates most efficiently and produces the best results. Experimentation helps in pinpointing these optimal settings.
- Accounting for Machine Variability: No two CNC machines are identical. Age, wear and tear, maintenance history, and even ambient conditions can influence a machine's performance. By experimenting, machinists can tailor their approach to the specific quirks of their machine.
- Tool Longevity: By trying out different speeds, feeds, and cutting strategies, machinists can find methods that maximize tool life, reducing costs and downtime associated with frequent tool changes.
- Optimizing Surface Finish: The desired surface finish can vary based on the application. Through experimentation, one can find the perfect balance of tool path, speed, and feed to achieve the required finish, be it mirror-smooth or textured.
- Adapting to New Materials: As industries evolve, new materials come to the forefront. Experimenting allows machinists to develop strategies for effectively machining unfamiliar materials.
- Innovative Techniques: Experimentation fosters innovation. By trying out unconventional methods or tool paths, machinists might stumble upon more efficient or precise ways of doing things.
- Safety and Predictability: By experimenting in controlled conditions, machinists can understand the limits of their setup, ensuring that they operate safely and avoid pushing the machine or tooling beyond its capabilities.
- Continuous Learning: The field of machining is ever-evolving. Regular experimentation ensures that machinists stay at the cutting edge (pun intended) of their craft, continually updating their skills and knowledge.
- Cost Efficiency: Through iterative testing, machinists can optimize processes to reduce waste, minimize errors, and improve production speed, leading to significant cost savings.
- Building Intuition: Over time, consistent experimentation helps machinists develop an intuitive sense of their work, enabling them to make on-the-fly adjustments and decisions with confidence.
While theory and guidelines provide a roadmap, experimentation is the vehicle that drives machinists to their destination of perfection. It's a blend of art and science, where data meets intuition. By embracing experimentation, machinists not only refine their current processes but also pave the way for future innovations in the realm of CNC machining.
Safety Considerations
Safety is paramount, acting as the linchpin that ensures the well-being of operators and the integrity of equipment. Proper safety measures, including the use of personal protective equipment, safeguard individuals from potential hazards like ejected chips or tool fragments.
Operating machines within safe parameters not only prolongs their lifespan but also guarantees the quality of the end product. A safety-first approach minimizes costly downtime, fosters a culture of responsibility, and meets both legal and ethical standards. In essence, while precision and efficiency drive machining, they should never overshadow the fundamental principle of safety.
Summing Up
As we've journeyed through the essentials of endmill speed setting, it's evident that every facet, from understanding surface speed to the nuances of material properties, plays a pivotal role in achieving machining excellence. The guidelines and principles discussed provide a roadmap, but it's the machinist's expertise, intuition, and willingness to experiment that truly brings these concepts to life. In this dynamic field, where technology continually evolves, staying updated and adaptable is the key to navigating the ever-changing landscape of machining challenges.
However, as we push the boundaries of what's possible in CNC machining, one principle remains timeless: the emphasis on safety. It's a reminder that while we strive for precision, efficiency, and innovation, the well-being of the people behind the machines is paramount. A holistic approach to machining, which balances technical prowess with a deep respect for safety and the material at hand, is what sets apart good machining practices from truly great ones. As we continue to explore and innovate in this realm, may we always prioritize knowledge, precision, and above all, safety, in our quest for perfection.
Happy Machining! 🛠️