The Great Spindle Cooling Debate
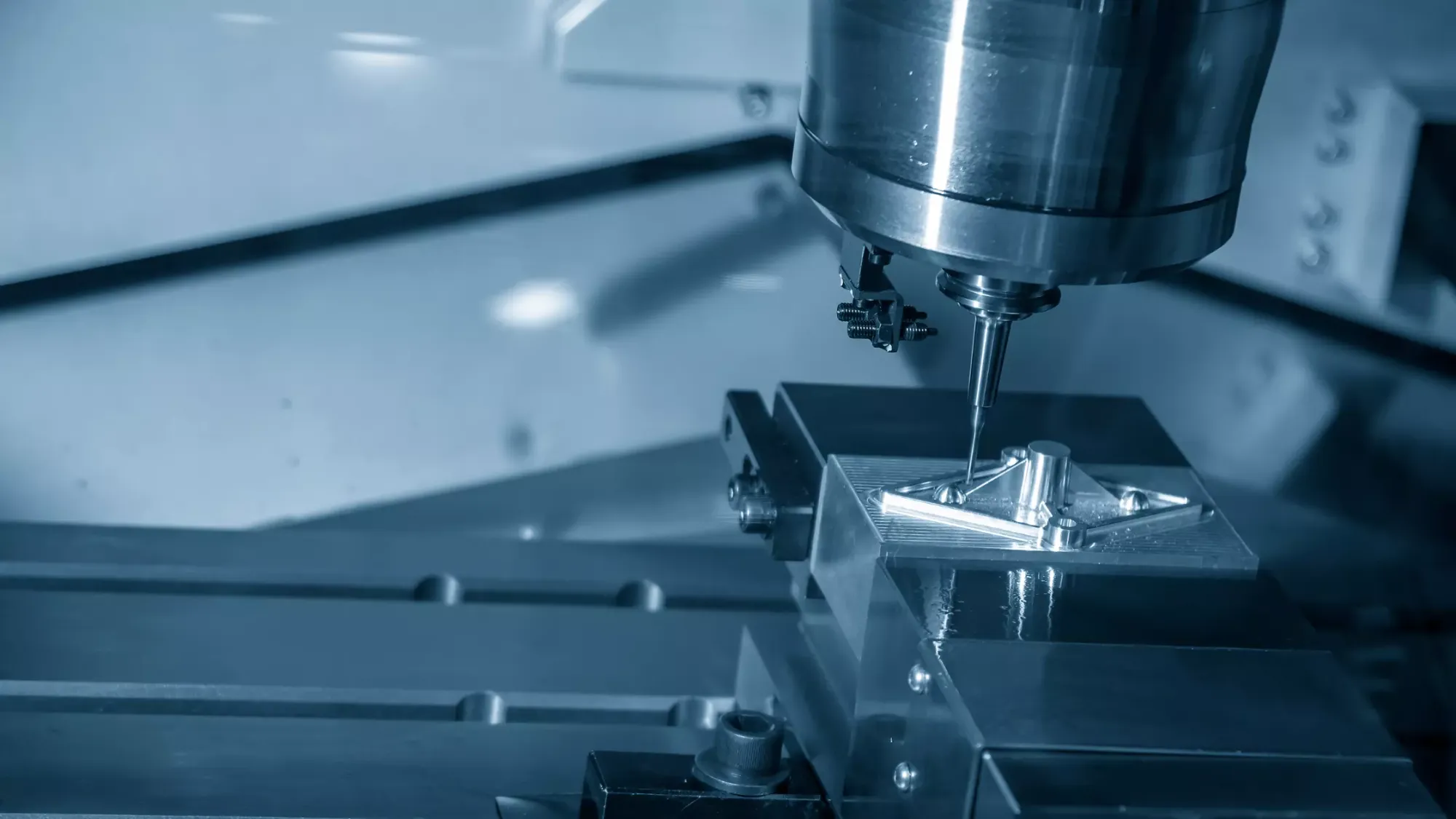
The world of CNC machining is vast, and the choices one makes can significantly impact efficiency, precision, and the overall quality of the final product. One such crucial decision is selecting the right spindle cooling system. Today, we'll delve deep into the two most common spindle cooling systems: air and water.
While seasoned machinists might have their preferred methods, newcomers often grapple with the benefits and drawbacks of air versus water-cooled spindles. And it's not just a matter of cold facts and figures; real-world, practical experiences shape these choices. So, whether you're a professional looking to optimize your setup or a beginner eager to make informed choices, this deep dive into air and water-cooled spindles aims to guide you through the maze of considerations. Let's embark on this enlightening journey and dissect the cooling cores of CNC!
Air-Cooled Spindles
Air-cooled spindles rely on ambient air and an integrated fan system to dissipate heat away from the spindle motor. As the spindle operates and generates heat, the built-in fan rotates, drawing in surrounding air and pushing it over the spindle, thereby cooling it. This mechanism is not only simple but also self-contained, making the spindle unit relatively compact.
Air-cooled spindles are a testament to the principle of simplicity. They offer a straightforward, low-maintenance cooling solution suitable for a wide range of applications.
Pros:
- Simplicity: The built-in fan means there's no need for external components like water pumps, reservoirs, or coolers. This direct method of cooling reduces the chance of external component failures.
- No Risk of Freezing: For workshops located in cooler climates, there's no risk of freezing, which could potentially damage equipment as is the case with water-cooled systems.
- Maintenance: Air-cooled spindles generally have fewer components that can fail or require replacement, translating to less routine maintenance. You don’t need to monitor fluid levels or check for algae.
Cons:
- Efficiency: Their cooling efficiency is limited by ambient temperature. In hot workshops or regions, the capacity of an air-cooled spindle to dissipate heat effectively reduces, which can lead to overheating issues during intense operations.
- Noise: Due to the in-built fan, air-cooled spindles can be notably louder than their water-cooled counterparts. This can be a concern in environments where noise pollution is a factor.
- Life Span: Potentially shorter lifespan when used in very demanding conditions due to the reduced efficiency of cooling, leading to increased wear and tear on the spindle components.
Temperature Regulation and Consistency:
One of the lesser-discussed aspects of air-cooled spindles is their temperature consistency. Because they rely on ambient air, their cooling efficiency can fluctuate with changing workshop temperatures. For tasks that require consistent machine temperatures, this might pose a challenge, especially in non-climate-controlled environments.
Flexibility and Portability:
Due to the absence of external cooling components, air-cooled spindles tend to be more portable. For operations that require relocating the machine or those that don't have a fixed workstation, an air-cooled spindle offers more flexibility.
Air-cooled spindles are a testament to the principle of simplicity. They offer a straightforward, low-maintenance cooling solution suitable for a wide range of applications. However, like all tools, understanding their strengths and weaknesses is crucial to harnessing their full potential. If your operations demand prolonged intensive tasks or if you're based in a particularly hot environment, considering these factors will be essential in making the most of an air-cooled spindle system.
Water-Cooled Spindles
Water-cooled spindles utilize a closed-loop system where water (or sometimes a water-glycol mix) circulates around the spindle motor to absorb and dissipate heat. This liquid coolant passes through a heat exchanger (or radiator), where it releases the absorbed heat before being pumped back to the spindle. This continuous circulation ensures consistent and efficient cooling, especially during long machining operations.
Water-cooled spindles are the embodiment of efficiency in the CNC machining world. They cater to professionals and enthusiasts who require consistent, prolonged performance without the pitfalls of overheating.
Pros:
- Efficiency: Water has a higher thermal conductivity than air, which allows for more efficient and rapid heat dissipation. This makes water-cooled spindles ideal for extended machining operations or when precision is paramount.
- Noise: Without the need for internal fans as in air-cooled variants, water-cooled spindles tend to operate more quietly. The only sound you might hear is the hum of the circulating pump, which is generally much softer than a fan's whir.
- Life Span: With superior cooling capabilities, the overall wear and tear on the spindle components is reduced, often leading to a longer operational lifespan.
- Consistent Performance: The closed-loop system maintains a more consistent temperature, ensuring stable machining conditions, which can be crucial for precision tasks.
Cons:
- Complexity: The setup for a water-cooled spindle is undeniably more complex, with the need for a coolant reservoir, pump, tubing, and heat exchanger. This might be daunting for beginners or those looking for plug-and-play solutions.
- Maintenance: Water-cooled systems require more regular check-ups. The coolant might need periodic replacement or topping up, and there's potential for algae growth or blockages if not properly maintained.
- Risk of Leaks: With any liquid-based system, there's always the risk of leaks, which can lead to potential damage or, in the worst case, a short circuit.
- Risk of Freezing: In colder environments, especially if the coolant is purely water, there's the potential for the coolant to freeze and damage the system.
Optimal Cooling and Precision:
Due to the high thermal conductivity of water, these spindles can maintain optimal operating temperatures even under strenuous conditions. This often results in better machining precision, especially for tasks that take extended periods, as the spindle remains cool throughout the operation.
Scalability and Upgrades:
A notable advantage of water-cooled systems is the potential for upgrades. As your needs evolve, you can enhance the efficiency of your cooling system by investing in a more substantial heat exchanger, a better pump, or even additives that improve the coolant's thermal properties.
Water-cooled spindles are the embodiment of efficiency in the CNC machining world. They cater to professionals and enthusiasts who require consistent, prolonged performance without the pitfalls of overheating. Their quiet operation is an added bonus. However, this efficiency comes with the price of added complexity and maintenance. Understanding these nuances will be the key to maximizing the benefits of a water-cooled spindle system. Whether you're looking for precision, consistency, or quiet operation, water-cooled spindles stand out as a formidable choice in the CNC realm.
Making the Decision
Choosing between air and water-cooled spindles is more than just a matter of specifications and features; it's about understanding your needs, your workshop's environment, and the long-term implications of your choice.
1. Understand Your Workshop Environment:
- Temperature & Climate: If your workshop is in a region with high ambient temperatures, the efficiency of an air-cooled spindle could be compromised. On the other hand, in extremely cold areas, water-cooled spindles could face freezing risks unless you use an anti-freeze coolant.
- Dust & Debris: Workshops with significant dust or debris might find that these particles clog up the cooling fins of an air-cooled spindle or dirty the radiator of a water-cooled system. Maintenance frequency might increase in such environments.
2. Evaluate Your Machining Needs:
- Duration of Operations: If your typical machining task spans several hours or even days without significant breaks, a water-cooled spindle's consistent cooling might be invaluable.
- Precision Requirements: Water-cooled spindles tend to maintain a more consistent temperature, reducing the risks of thermal expansion that might compromise precision.
- Flexibility: For those who might need to relocate their machinery or work on different sites, the self-contained nature of air-cooled spindles offers greater portability.
3. Consider Long-term Costs:
- Maintenance & Repairs: While water-cooled systems might require more regular maintenance, air-cooled systems might face quicker wear and tear in intensive conditions, leading to potential replacements or repairs.
- Energy Consumption: Water-cooled spindles, with their efficient cooling, can sometimes be more energy-efficient in the long run. Check the power ratings and consumption statistics before making a choice.
4. Think about Future Scalability:
As your operations grow or your needs change, will your chosen spindle cooling system adapt? Water-cooled systems, for instance, allow for upgrades to the pump or heat exchanger, offering more scalability. Assess whether your choice will stand the test of time and evolving needs.
5. Noise Sensitivity & Workspace Comfort:
Are you working in a shared space or an environment where noise levels matter? Water-cooled spindles are generally quieter. Also, consider the comfort of operators. A constantly running air-cooled spindle in a small, enclosed space might raise ambient temperatures, affecting operator comfort.
6. Seek Peer Reviews & Expert Opinions:
Sometimes, the best insights come from those who've walked the path before you. Reach out to fellow machinists, join CNC forums, or attend workshops. Real-world experiences can offer invaluable perspectives.
Selecting between air and water-cooled spindles is a multifaceted decision that requires a thorough understanding of both your immediate and future needs. Take the time to assess, research, and reflect. Remember, the best decisions are informed ones, and the right choice today will pave the way for smoother machining tomorrow.
Cost Comparison
When it comes to integrating machinery into your workshop, one of the primary considerations is, without doubt, cost. Both upfront costs and long-term expenses play a crucial role in determining the overall value of your investment. Let’s break down the cost elements for both types of spindles:
1. Initial Investment:
Air-Cooled Spindles: Generally, air-cooled spindles can be less expensive upfront. Their design is straightforward, with fewer components, which usually translates to a lower initial cost. Typical price ranges might vary depending on the spindle's power rating and brand, but for many hobbyists and small-scale operations, air-cooled spindles offer a cost-effective entry point.
Water-Cooled Spindles: These usually come at a premium, especially when you account for all the necessary components – the spindle itself, pump, reservoir, heat exchanger, and tubing. The comprehensive setup ensures efficient cooling, but it also means a heftier initial investment.
2. Operational Costs:
Air-Cooled Spindles: These systems might consume more power over time, especially in warmer environments where the spindle's fan must work harder to maintain optimal temperatures. Additionally, if an air-cooled spindle is not efficient enough for prolonged operations, it might require breaks, potentially leading to longer project durations.
Water-Cooled Spindles: Generally more energy-efficient due to the superior heat transfer properties of water. However, there will be additional electricity costs for running the water pump, though these are often negligible. The efficiency of water-cooled spindles means shorter project durations and potentially lower electricity bills over extended periods.
3. Maintenance and Repairs:
Air-Cooled Spindles: While these have fewer components to fail, once they do, replacements can sometimes be expensive. Also, in challenging environments, the built-in fans can accumulate dust and debris, potentially leading to increased wear and shortening the system's lifespan.
Water-Cooled Spindles: Maintenance might involve regular coolant checks, cleaning the reservoir to prevent algae growth, and ensuring the pump and tubing remain in top condition. However, since individual components can be replaced, you might find that maintenance costs are spread out, rather than facing a significant one-off replacement fee.
4. Long-Term Value:
When assessing costs, it's crucial to think long-term. While air-cooled spindles might seem cost-effective initially, the potential for increased energy consumption and earlier wear-out can offset the initial savings. On the other hand, the higher upfront investment for water-cooled spindles might be justified by their efficiency, longevity, and precision.
Cost is undeniably a significant factor in choosing between air and water-cooled spindles, but it shouldn’t be the only one. Weigh the immediate costs against long-term value, consider your operational needs, and estimate the maintenance and repair implications. By taking a comprehensive view of expenses, both immediate and long-term, you'll be in a better position to make an informed investment in your CNC machining endeavors.
Conclusion
Whether you're a seasoned machinist or just getting started, the choice between air and water-cooled spindles is significant. Weigh the pros and cons, consider your workshop's specifics, and make an informed decision. Both systems have their merits, and the best choice always boils down to individual needs. Happy machining!
I hope this article sheds some light on the practical aspects of selecting between air and water-cooled spindles. Remember, the tools we choose are only as good as our understanding of how best to use them. Stay curious and keep exploring!